Dai tempi di fermo macchina ai tempi di funzionamento
2022-05-30
3 min read
“Se non è rotto, non aggiustarlo” è una frase accattivante, ma non è una buona regola pratica. I tempi di fermo macchina non pianificati e la scarsa qualità degli asset costano alle industrie manifatturiere e di trasformazione circa 20-60 miliardi di dollari all'anno. Purtroppo, tale riluttanza ad adottare nuove tecnologie, dovuta in parte ai costi iniziali, ha ostacolato i progressi nelle operazioni.
Anche se possono essere inevitabili, i guasti alle apparecchiature non devono causare tempi di inattività prolungati, erodere i profitti o determinare uno sforamento del budget per i produttori. Gli impianti di produzione odierni sono molto più complessi che in passato, composti da reti di dati, hardware integrato e una serie di sistemi automatizzati. Di conseguenza, la maggior parte dei produttori non dispone di metodologie di manutenzione adeguate. Infatti, secondo un report di Infraspeak, il 93% delle aziende ritiene che i propri processi di manutenzione non siano molto efficienti.
La manutenzione predittiva è un modo per prevedere ogni possibile scenario di guasto dell'hardware, identificando quando occorre effettuare la manutenzione e allertando il personale addetto in caso di necessità, oltre a fornire soluzioni preventive.
Chiunque operi all'interno dell'ecosistema manifatturiero capirà che i guasti e i cedimenti si verificano quasi ogni giorno. L'obiettivo della manutenzione predittiva non è solo prevenire o ridurre questi guasti, ma anche aiutare gli stabilimenti di produzione a raggiungere standard di efficienza elevati e a fornire nel contempo prodotti di qualità. Un programma di manutenzione predittiva può ridurre i guasti imprevisti fino al 90%, eliminando quasi del tutto i cedimenti.
Per eseguire la produzione predittiva in modo efficace, il responsabile dello stabilimento deve raccogliere il maggior numero di dati possibile. È un'operazione fondamentale quando si implementa una strategia di manutenzione preventiva, dato che maggiore è il numero di dati disponibili da analizzare, più accurate saranno le previsioni sui guasti.
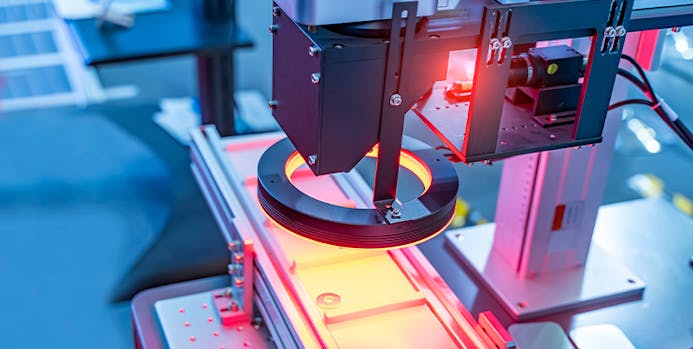
Percepire il pericolo
L'uso di sensori intelligenti potrebbe rappresentare un buon punto di partenza. I sensori intelligenti, insieme agli algoritmi di apprendimento automatico, aiutano a rilevare le anomalie nelle macchine industriali. Ad esempio, i sensori intelligenti che raccolgono dati in ambienti IoT industriali possono tenere traccia della temperatura, identificando i componenti usurati come i circuiti elettrici malfunzionanti.
Analogamente, i sensori intelligenti specializzati possono eseguire l'analisi delle vibrazioni su un particolare componente, identificando eventuali casi di disallineamento, alberi piegati o altri problemi del motore. Partendo da questi dati, i produttori possono creare un'analisi delle risorse critiche per stabilire le modalità di guasto. In questo caso, l'attenzione è posta sulla frequenza dei guasti, sulla gravità dei guasti alla macchina e sulla difficoltà di individuarli.
Collegando i dispositivi di monitoraggio delle condizioni a un CMMS, i responsabili di stabilimento possono impostare avvisi per informare il personale addetto alla manutenzione di eventuali guasti o anomalie nelle apparecchiature. Ciò offre l'opportunità di pianificare la manutenzione programmata nel momento in cui le parti devono essere sostituite, eliminando la possibilità di gravi cedimenti.
Ad esempio, la tecnologia dei sensori può essere integrata con diversi prodotti come connettori, tubi e tubazioni, pompe, motori, attuatori e filtri. In questo caso, alcuni dei dati diagnostici generati dalle valvole di controllo potrebbero essere fondamentali per la risoluzione dei problemi di alimentazione.
Le macchine recenti di solito dispongono di diverse opzioni per l'acquisizione di dati in tempo reale, ma anche le apparecchiature esistenti possono essere rimodernate con sensori aggiuntivi poco costosi. La manutenzione predittiva può essere una risorsa vitale quando si tratta di asset che invecchiano e che richiedono un'attenta pianificazione per reperire parti di ricambio obsolete.
Anche se i guasti delle apparecchiature sono in una certa misura inevitabili, non dovrebbero causare tempi di fermo macchina imprevisti e una scarsa qualità degli asset, costando alle industrie di produzione e trasformazione miliardi ogni anno. Al contrario, un piano di manutenzione predittiva completo ed efficace contribuirà a prevenire e ridurre in modo significativo i tempi di fermo macchina, incrementando al contempo i profitti dello stabilimento attraverso l'aumento dei tempi di funzionamento.