- Inicio >
- Industrias >
- Ingeniería y mantenimiento >
-
Industry Report
Ingeniería y mantenimiento
Maintenance, repair and operations engineers have a laser-like focus on avoiding unexpected downtime. Intense efforts are made to keep shop floor machinery in optimal condition, ensuring that production lines do not suddenly grind to a halt. Well-maintained equipment is less likely to break down and is typically more productive, but maintenance comes at a cost. Scheduled downtime and associated lost production, along with human resources in both hours and skill levels, are frequently how a maintenance programme is evaluated.
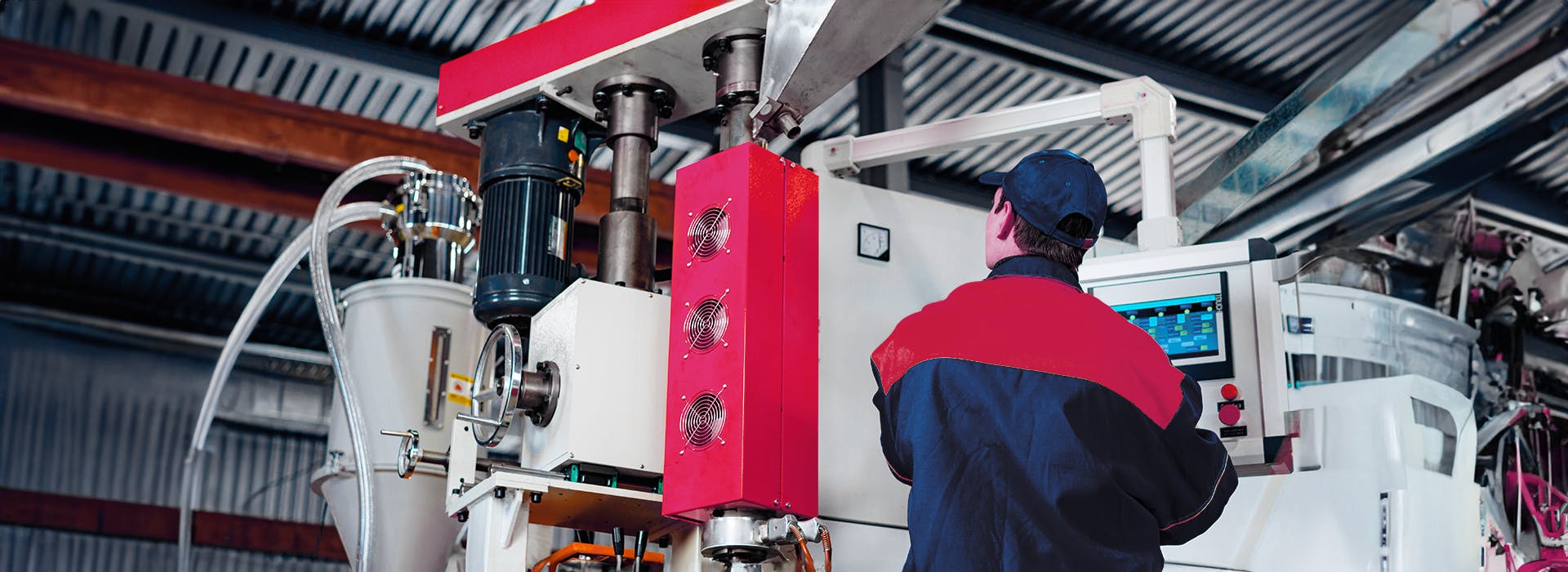
- 1 Introduction to condition-based maintenance with real-time monitoring
- 2 Evaluating sensor technologies for real-time monitoring
- 3 Making condition-based monitoring work
- 4 Seven steps to successful condition-based maintenance
- 5 Your partner in condition-based maintenance
- 6 What next for condition-based maintenance with real-time monitoring?
- 7 Why condition-based maintenance with real-time monitoring makes sense
1. Introduction to condition-based maintenance with real-time monitoring
Maintenance, repair and operations engineers have a laser-like focus on avoiding unexpected downtime. Intense efforts are made to keep shop floor machinery in optimal condition, ensuring that production lines do not suddenly grind to a halt.
Well-maintained equipment is less likely to break down and is typically more productive, but maintenance comes at a cost. Scheduled downtime and associated lost production, along with human resources in both hours and skill levels, are frequently how a maintenance programme is evaluated.
However, advances in technologies such as sensors and data analytics have seen condition-based maintenance based on real-time monitoring emerge as a powerful tool in the more connected factories of the future. This approach allows for exceptional levels of equipment performance visibility and can provide an intelligent solution that maximises equipment uptime. It is a strategy that can help manufacturing operations stay as productive and profitable as possible – something that all maintenance professionals in management and frontline roles want to help ensure.
What is condition-based maintenance with real-time monitoring?
Condition-based maintenance techniques involve the real-time monitoring of an asset, providing specific indicators to determine what maintenance needs to be performed and when. With condition-based maintenance with real-time monitoring, engineers can avoid unnecessary production loss with an up-to-the-minute assessment of equipment conditions through real-time monitoring and prior warning of failures. Using sensors to measure vibration and temperature, as well as many other parameters, for equipment health monitoring it becomes apparent when a machine is running normally but also when it is not.
This revolution in condition-based maintenance has come about mainly through advances in sensors and connectivity, but it is also enabled by the Internet of Things (IoT) and is increasingly improving due to machine learning (ML) and Artificial Intelligence (AI).
Understanding the significance of this technology means appreciating both the importance of maintenance as well as the methods condition-based maintenance can replace.
Why maintenance can be a costly business
Huge numbers have been put forward for how much the annual maintenance bill in manufacturing – a report on the US market estimated a figure of $220 billion [1]. But to give the issue more context, a recent survey [2] found that almost half of companies in the US spent 21-40% of their operating budget on cleaning and maintenance equipment/supplies. While there is enormous variance, this means a typical plant with a $10 million operating budget would be spending around $3 million on cleaning and maintenance activities.
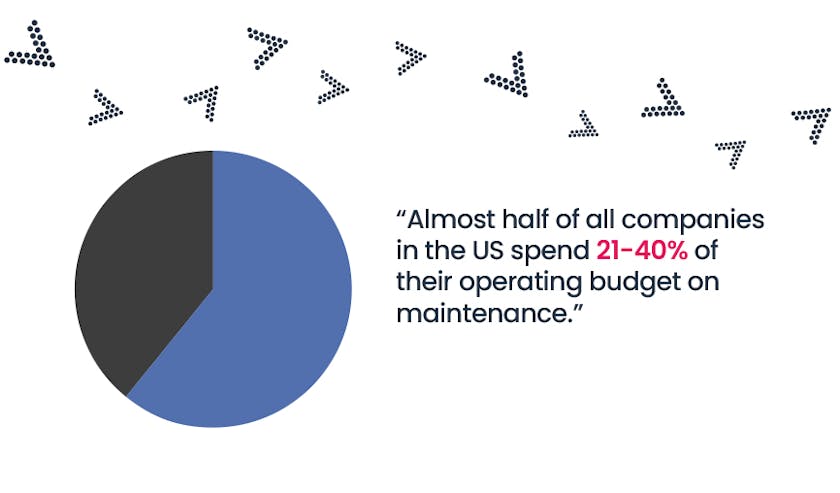
How reactive maintenance is not always suitable
‘If it isn’t broke, don’t fix it’ is an established maxim many industrial sites still use, but there are many ways of approaching maintenance, with the oldest being reactive maintenance. Also termed ‘run to failure’ it simply means running an industrial asset until it breaks down, and when it does break down, then it either needs to be immediately replaced or repaired.
Reactive maintenance has the appeal of requiring no upfront or ongoing costs and few, if any, dedicated personnel. When the asset does break, conversely, it requires an immediate input of engineering time and finance, with the potential of impacting other operations. It is a strategy that has merit on non-critical equipment. A Plant Engineering Maintenance Study [3] indicated that 61% of manufacturing companies still used reactive maintenance for at least part of their operations. The simplest example would be the light bulb – it is only replaced when it blows. But it is not a philosophy that scales well, as the larger or more complex the equipment, the greater the ramifications of it not working as it should.
The consequences of using reactive maintenance throughout the plant, rather than condition-based maintenance with real-time monitoring, can be severe. Unpredicted failures are likely to cause unplanned downtime, affecting the productivity of the entire operation. Costs can be daunting, especially if equipment needs to be replaced rather than just repaired, and the skills to do repairs may not be immediately available.
It is also worth considering that poorly maintained equipment can be inefficient, resulting in unnecessarily high energy costs and a drop in productivity. Product quality can also be impacted by poorly maintained production equipment not working within specification, with the potential consequences of customer dissatisfaction or expensive product recalls.
Understanding scheduled and preventative maintenance
One way to minimise the chances of unplanned stoppages is to have a scheduled programme of equipment health monitoring. This also has the advantage of allowing a predictable budget and the appropriate staffing for maintenance operations.
A scheduled maintenance programme should be specific to an industrial site and all the equipment within it. Using historical data (or OEM information for new equipment) from all assets – previous maintenance and breakdowns along with running performance – a programme can be constructed that will decrease the likelihood of machine failure and smooth maintenance and repair costs.
Good scheduled maintenance should be able to evolve as more information comes in. A pump that keeps breaking down due to leaking seals, bearing failure or improper lubrication will not have been maintained often enough, and the schedule should be tightened accordingly. This re-evaluation requires human instinct and input to update the schedule, while ongoing assessment can add structure.
Condition-based maintenance vs predictive maintenance
Preventative maintenance relies on the accuracy of historical data. On the other hand, predictive maintenance uses live machine health monitoring data to determine when an asset needs to be maintained or replaced. This is where condition-based maintenance with real-time monitoring comes in.
Sensor and connectivity technology advances have made it feasible to collect real-time data from every asset. Analysing the data and comparing it to historical and expected performance can reveal whether a machine operates normally or drifts toward its performance limits. Using this information for equipment health monitoring, corrective condition-based maintenance can be planned before the machine fails and also at a time when it suits maintenance staff and factory/production schedules. It also means that equipment is not taken out of operation for maintenance more often than is required – scheduled maintenance is often unnecessary. Perversely, over-maintained machines can age more quickly than optimally maintained ones; for example, adding grease to a sufficiently lubricated part just because of the schedule can reduce machine efficiency and increase contamination.
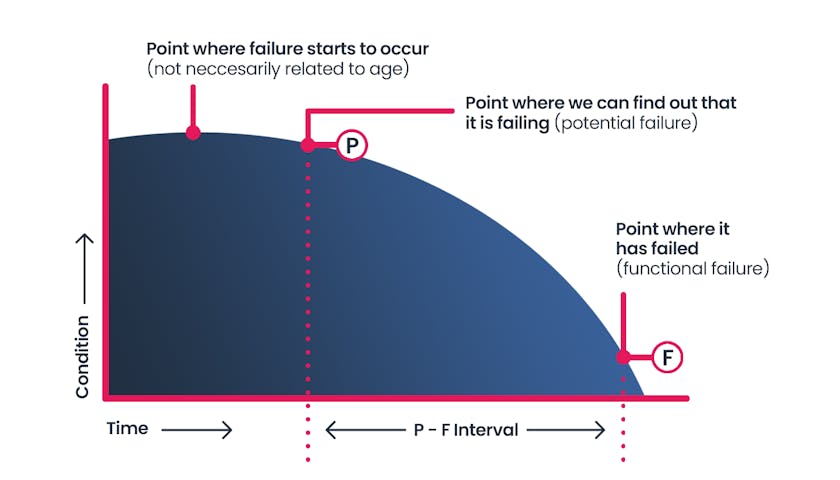
The prevention-failure (P-F) curve (above) explains the importance of maintenance timing in preventing machine failure and why condition-based maintenance can be such a valuable tool. The time to get to point P can vary enormously from one machine to another, and that is what creates doubt about the value of maintenance schedules. However, the critical factor in the above diagram is the P-F Interval. As long as the period between asset monitoring is less than the P-F Interval, a machine should, in theory, always be prevented from reaching the point of failure.
Condition-based maintenance being largely, although not exclusively, a real-time monitoring and continuous machine health monitoring tool, enables the identification of potential problems close to when machine performance begins to drop - point P. It thus provides the longest maintenance window and more flexibility around scheduling the necessary downtime. Typically, the cost of repairing a machine rises as its condition deteriorates; the closer a fault is detected to point P, the cheaper the maintenance or repair will be. Delaying maintenance until point P (the first point at which that maintenance is required) prevents the unnecessary cost and time involved in maintaining that asset under scheduled or preventative maintenance methodologies.
Catching potential problems early benefits factory uptime, the biggest advantage of condition-based maintenance, and streamlines maintenance costs and staffing activities. It also improves asset longevity, can make the factory safer, and even has beneficial consequences for product quality and customer satisfaction.
In terms of the benefits of condition-based monitoring, McKinsey anecdotally takes the example of a large technology manufacturer that introduced a condition-based maintenance framework pulling data from several different sources, including Industrial IoT (IIoT) devices and a historical service database. The consequent savings in reduced labour, downtime, parts, and other related costs were around 30%.
Indeed, the primary benefits of condition-based maintenance have been outlined by some of the world’s leading technology companies. Research and data from IBM in development of its Maximo intelligent asset management suite has led to it citing five tangible benefits that are applicable across manufacturing organisations:
- Prevention of equipment failures and downtime.
- Extension of asset lifespan.
- Improved safety through enhanced issue detection.
- Reduced maintenance costs.
- Improved maintenance efficiency.
IBM suggests that the combined benefits are substantial: it says that condition-based and predictive maintenance alone can reduce costs by 15% – 20% and improve asset availability by 20%.
Condition-based maintenance in action: how a UK manufacturer saved £25,000
Warwickshire-based animal feed and refined oil manufacturer Yelo has effectively deployed condition-based maintenance into its operations.
Working with partner AVT Reliability, it wanted to identify potential problems so pre-emptive action could be taken, averting unplanned equipment failure.
A digital condition monitoring and asset management project involving a wireless tri-axial vibration and temperature sensor was fixed to assets deemed critical enough to require consistent evaluation. The sensor records at frequent intervals, with the data accessible via a secure web browser, while monthly reports indicating high-priority action are also produced.
Yelo says that the actions raised by the condition-based maintenance system saved more than £25,000 in wasted costs in the implementation phase alone. Early detection of developing failure modes has allowed maintenance teams to be more proactive and minimise any potential disruption to operations.
The project was conceived and delivered in a matter of weeks and provided the foundation for a sustainable long-term condition-based maintenance programme. More details of the case study can be found here on the CBM Connect website, which provides educational articles, videos and podcasts on condition-based maintenance.
Getting started with condition-based maintenance
While the long-term benefits of adopting a system based on condition-based monitoring with real-time monitoring for a modern factory are considerable, there are obstacles to overcome when establishing a condition-based maintenance strategy. The main one is the upfront costs involved. Although sensors for machine health monitoring have become much more affordable, they represent a considerable initial outlay, as do the network and software systems they plug into.
Designing your condition-based maintenance network real-time monitoring, from both hardware and software perspectives, may also be daunting. There may be some alterations required to the plant, although most sensor technologies are non-intrusive, so incorporating them is not a significant feat of engineering. Choosing the right technologies for real-time monitoring of the right assets takes both knowledge and time. However, there is considerable knowledge in the supplier base. Solutions for condition-based monitoring are available from the largest automation providers to smaller specialists in the field.
Typically, although not always, ongoing use of the system will be by in-house engineers, so training will be necessary. And a final consideration is that condition-based maintenance with real-time monitoring must be done ‘on demand’. Although condition-based maintenance acts as an advance warning system through equipment downtime analysis and provides a window during which remedial activities can occur, it is not as predictable as the workflow in a scheduled maintenance regime.
As with the light bulb example above, it is also worth noting that not all equipment benefits from condition-based maintenance methodology. Almost 30% of industrial equipment does not benefit from condition-based monitoring with real-time monitoring, according to Hashemian and Bean [5].
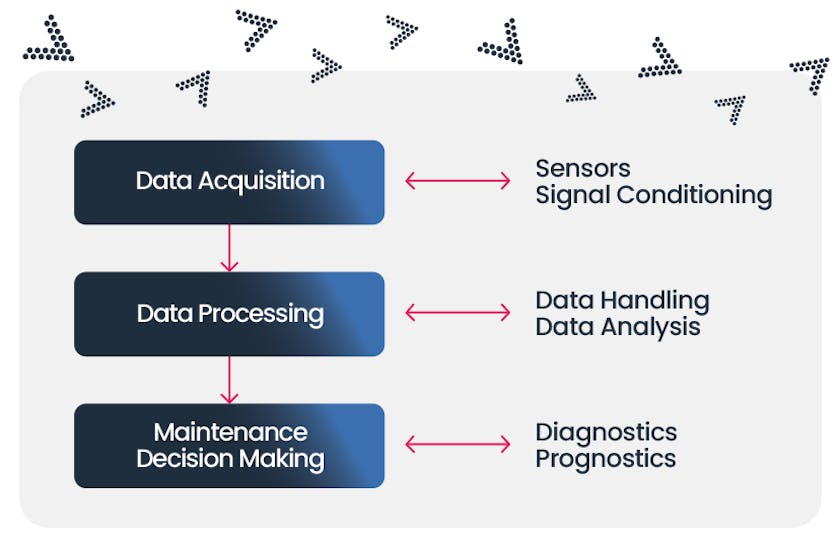
A predictive maintenance system can be broken down broadly into the three areas above.
A host of sensor options can reveal an asset's health, the most common of which are vibration, temperature, noise, radiography, pressure and oil analysis. Sensor technology and what information they can provide are detailed below.
Open standards in sensors as well as in the fieldbus networks mean the connection is generally straightforward on existing communications infrastructure. The emergence of wireless networks and the IIoT has also enabled condition-based monitoring with real-time monitoring to be employed in applications where some of the assets may be disparate – mineral processing and water works as examples. IIoT solutions are becoming the norm in most applications as they offer ease of set-up and flexibility.
As with the hardware, the software generally benefits from open standards. There is plenty of choice of which package to choose from, and third-party help is widely available to ensure integration of the system as well as outputs that are meaningful for the user. This typically involves alerts for assets running outside set parameters and dashboards for easy system supervision.
Another of the enabling technologies with condition-based maintenance and real-time monitoring is AI, or more accurately, ML. By using all historical performance data from each piece of equipment, the model of that machine’s behaviour becomes more accurate as time goes on. Performance variances are better understood, and maintenance requirements can be tailored more accurately.
ML-enabled information provides details of the condition a machine is in, its current efficiency and likely time to failure, but ultimately it will be a human decision as to what maintenance is done and at what time. Condition-based monitoring allows that decision to be fully informed.
2. Evaluating sensor technologies for real-time monitoring
The core enabling technology behind condition-based maintenance and the real-time monitoring it allows lies in the sensors. No one sensor type fulfils all the demands of real-time monitoring and equipment downtime analysis. Specific sensors are of more use, for example, for monitoring rotating machines, while others better suit valves and cabling.
Let’s look at the various sensors for real-time monitoring and the information they can provide.
Vibration sensors for real-time monitoring
Vibration sensors are one of the most valuable tools for real-time monitoring and usually lie at the core of condition-monitoring techniques in industrial environments. They are beneficial for monitoring rotating equipment and, like most sensors, can be simply fitted externally, ideally on the casing around where the bearing is located.
A rotating machine ideally does not create much vibration. The smoother it runs, the better it is performing. Defects like a bent shaft, worn bearings and damaged blades can cause very slight irregularities in the vibration signature, and these can be picked up by the vibration monitor and provide real-time information on machine condition.
The typical vibration monitor is a piezo accelerometer. Simply put, this converts the stress caused by vibration into an electric charge proportional to the vibration. They are robust, reliable and are proven to work across a wide range of frequencies.
The alternative is micro-electromechanical system (MEMS) accelerometers. These have lagged behind their piezo counterparts mainly on the reading noise that they produce. Piezo accelerometers have traditionally provided a better signal-to-noise ratio (SNR). This capability is an important factor in determining the quality of results and the usefulness of the real-time monitoring system. MEMS technology has improved significantly over recent years and is often comparable to piezo devices except at the highest frequencies (typically over 20kHz).
Where MEMS technology is proving particularly useful is for wireless applications. It has low power requirements and can be run on a battery, so it lends itself to the IIoT environment.
When selecting which accelerometer type to use for real-time monitoring, it is worth exploring and taking advice on both options, with signal quality being the starting point.
Acoustic and ultrasonic sensors for real-time monitoring
While the vibration signature of a machine may change or drift over time, the same is also true of the noise it emits. When the asset has bearing or gear damage, lubrication issues or any other mechanical fault, it will release high-frequency sounds, and acoustic sensors can pick up on that sound signature. Analysis of real-time monitoring data can reveal maintenance or failure issues. Structure-mounted sensors are used for direct machine health monitoring.
While acoustic sensors just listen to the sounds of the process they monitor, ultrasonic sensors go a step further and emit very high-frequency sound waves and then pick up the return waveforms. These can be used in real-time monitoring for analysing the structural integrity of materials and machines such as damaged or cracked housings.
Another use for ultrasonic sensors is in non-contact (airborne) applications, where they can be used to detect leaks in compressed gas systems. Airborne ultrasonics can also detect arcing and corona for electrical systems.
Acoustic sensors pick up sound audible to humans, while ultrasonics are at frequencies too high for humans to hear.
Temperature sensors for real-time monitoring
Temperature is another signal of asset condition. Bearing wear, lubrication levels (over as well as under), changes in airflow, and wear at any friction points can result in deviations from the typical running temperature. Thus, it can be a useful indicator for condition-based maintenance strategies using real-time monitoring techniques. Typical applications are for equipment with moving or rotating parts like pumps, fans and motors.
Temperature sensors are already standard in some industrial plants as they play an essential role in the process – food and beverage and chemical industries for example. In these cases, the sensors may need to be embedded within the equipment so that they can be operated in process fluid. The sensors we are looking at for condition-based maintenance using real-time monitoring can be externally mounted on the asset.
Thermal sensors work by measuring the voltage difference or resistance between two diodes caused by a change in temperature, and mapping that change to a temperature value. There are several types of thermal sensors, the most frequently used being thermocouples, thermistors, Resistance Temperature Detector (RTD) and semiconductor-based sensors.
The most common type of sensor in very high-temperature applications - for example, those that involve furnaces or material processing - are thermocouples, which are capable of withstanding heat of over 2000 degrees Celsius. These sensors are small, rugged and responsive. An ideal condition-based maintenance application for thermocouples is within an aircraft engine with extreme temperatures and a hostile environment. However, thermocouples need careful selection, installation and calibration to ensure that they remain accurate and do not drift over time.
RTD sensors are more accurate than thermocouples, benefiting from their platinum-based construction to give them the accuracy and repeatability required in many processing industries. Not as small as thermocouples and with a lower temperature range (generally up to 650 degrees Celsius), RTD sensors not as tolerant to vibration, restricting its use on some condition-based maintenance tasks.
Thermistors are not made of platinum and can be designed to have specific temperature ranges depending on the alloys used. This means they are often designed for specific temperature ranges and have particular applications. They are typically lower temperatures (300 degrees Celsius max), but like RTD sensors also have limitations on the environmental conditions they must withstand.
With the advantages of being integrated into printed circuit boards (PCBs), semiconductor-based thermal sensors are restricted by their temperature range (under 150 degrees Celsius). They generally do not respond as quickly as other sensors and are not the most accurate, but do suit IIoT, edge computing-type applications.
Choosing which type of temperature sensor for your condition-based maintenance system and the need to perform real-time monitoring becomes a balance. Thermocouples have the highest temperature range and are the most durable. RTDs and thermistors can only operate at lower temperatures but are more accurate. Semiconductors can be built into the control and communications board.
It is worth noting that the most common reason for thermal sensors failing is thermal damage – always specify with plenty of slack.

Infrared sensors for real-time monitoring
Also under the thermal sensor category are the non-contact infrared sensors. These work by measuring the thermal radiation emitted by a heat source and are particularly useful in detecting electrical as well as some mechanical faults.
While static infrared cameras can be set up to monitor a specific asset, they are instrumental in conducting site surveys. A structured survey encompassing all equipment historically most likely to fail or is most crucial to the operation can be performed every few months, weeks or days. Strictly speaking, this becomes structured or preventative maintenance, but it can play a useful role in a CBM monitoring programme.
A handy application can be in monitoring fuse boxes and electrical or control panels, where excess heat can indicate a loose connection or pending failure. A whole array of static sensors would be required to cover the same area.
Doing quick sweeps of large amounts of mechanical equipment is another helpful application, conveyors being a prime example. Infrared sensors are more expensive than other temperature sensors, but they have advantages in terms of coverage, flexibility and the types of faults they can detect.
Magnetic field sensors for real-time monitoring
Also aimed at machine health monitoring for motors are magnetic field sensors. Motors have a signature magnetic field around them, which is disrupted by irregular function. These sensors are non-contact and must be correctly orientated to take measurements either parallel or perpendicular to the motor shaft. Their performance is also tied in with temperature, so temperature readings must be taken and compensated for when analysing the readings. For this reason, many magnetic field sensors have built-in temperature sensors.
Oil analysis sensors for real-time monitoring
Analysing the oil can provide a revealing insight into what is happening inside the machine. A worn bearing will leave tell-tale particulate information in an oil sample. Equally, moisture ingress or contamination can be picked up. Lubricants that have become too viscous also stop performing efficiently, so this is another parameter that the oil sensor can monitor. Some oil sensors involve sampling the machine lubricant, which must then be sent away for analysis, while semi-automatic options allow analysis within the factory. However, inline oil sensors can also yield real-time information and play a part in a condition-based maintenance system.
How to pick the right sensors
There is a wide choice of sensors for condition-based maintenance and real-time monitoring techniques; all will have advantages, disadvantages and compromises. The most typical sensor for rotating machinery is the piezo accelerometer. This is partly because it has been the traditional – and cheapest - choice and partially because an excessively vibrating machine can easily be understood to be in danger of failure. But there are drawbacks as well, as an increasing trend towards wireless systems means sensors may have to be battery-powered, or at least are easier to manage if they are. And piezo accelerometers are not the most low-power option.
There is a compromise to be made with performance, power, cost and application, and all sensors used for equipment health monitoring potentially have a part to play. The best starting point for condition-based maintenance and real-time monitoring is to determine what items of the plant are the most critical and those that are most likely to fail, and then choose the most suitable sensors for those.
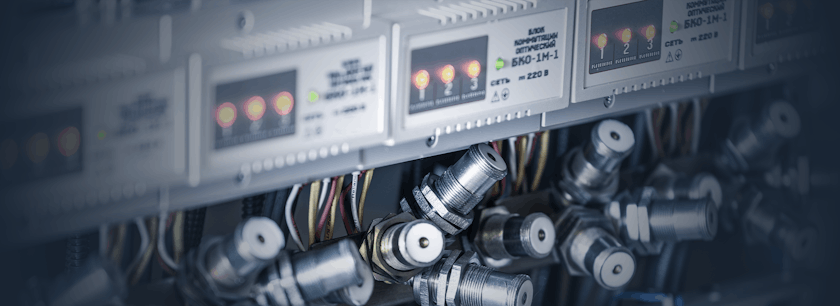
Visualising your data for condition-based monitoring
The heart of the condition-based monitoring system is the software, also frequently termed the CMMS, computerised maintenance management system. This is the software that helps manage assets and schedule maintenance. It is the central hub for all the collected data, analysing it and presenting it in the most useful way for the maintenance engineer.
A software-based data model for each asset will include historical performance, failure and maintenance records, tolerance levels and any other information relevant to the efficient running of the machine.
This information is then combined with the feed of real-time data received from the sensors, providing a complete historical and ongoing report on the performance of the asset. When performance drifts outside set parameters, a warning can be sent to alert staff when maintenance is required, or in extreme cases (if the condition-based maintenance system with real-time monitoring is integrated with the factory control system), automatically shut down a machine until remedial action is undertaken. The operational tolerances, the nature of alerts and subsequent automated actions will all be determined at system set-up and can then be optimised over time.
Intuitive dashboards for condition-based maintenance programmes can monitor the system in real-time, giving visual indications of where potential problems might be developing. Real-time monitoring dashboards can be quite a personal thing – some people like schematics of the plant with red flashing lights highlighting problem areas, while others prefer tables of data. It is a matter of personal preference what data is shown, and in what format, and dashboard add-ons are readily available for any application.
In the example below [6], ABB installed ABB Ability Asset Vista Conditioning Monitoring at the CELSA steel mill in Barcelona. The application monitors the health of various production assets, including automation, instrumentation, electrical, mechanical and/or process equipment. It offers CELSA a complete overview of its production assets’ health, avoiding unnecessary maintenance, reducing exposure to hazardous areas and speeding up repairs.
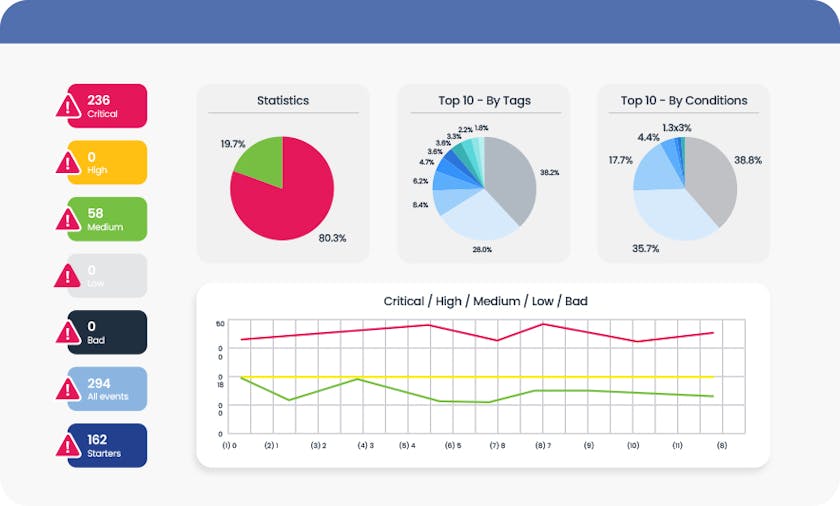
There are many options on the market for choosing condition-based maintenance software, and condition-based maintenance with real-time monitoring itself is a methodology that works across many industries, including manufacturing, transportation, energy, telecommunications and chemicals processing. It is worth ensuring that the software package selected has been used before in your specific sector and is compatible with whatever Enterprise Resource Planning (ERP) or Manufacturing Execution Systems (MES) systems you operate.

3. Making condition-based monitoring work
Few things ever work in any business environment unless there is buy-in from all stakeholders in the project. In the case of condition-based monitoring, it must be supported by management, the IT department, the engineers whose plant it will be used on and the maintenance staff who need to buy into the new regime. As with any change, there is a danger of resistance, so a plan of what the new condition-based monitoring system involves and why it is being introduced will be critical to its successful implementation.
Hopefully, the advantages of allowing for equipment downtime analysis will become immediately apparent to all involved, but there is always the possibility that some may see it as a threat to their jobs. A maintenance engineer, entrenched in the scheduled maintenance mentality, may see condition-based monitoring as threatening their careers or personal routines. Quite the opposite, condition-based maintenance is recognised as a supporting tool for engineers that allows them to work more efficiently and deliver greater value.
That said, information and communication are essential to success, as is knowledge of the new condition-based monitoring system and how it works. Key personnel – those involved in specifying, commissioning - must be adequately trained.
An important realisation here is that while condition-based monitoring can be integrated into a broader plant control system and be used as part of that control system, condition-based monitoring is fundamentally a tool. It is there to tell engineers how their assets are performing. It can then be used to analyse the problems and advise how to rectify them, but the action taken is at the engineer’s discretion. That engineer needs to have full technical knowledge of the machinery, a complete understanding of what the condition-based monitoring system covers and does not cover, what the data means and reasons for ambiguities, and the ability to troubleshoot should issues arise.
For these reasons, training key personnel from the outset is a good idea to maximise the benefit of a condition-based monitoring strategy and perform effective machine downtime monitoring. Guidance and training will often be available from the hardware and software suppliers. There is a large amount of knowledge in the supplier base – make the most of it. There are also courses on condition-based monitoring run (by a host of specialist training companies) on a non-proprietorial basis that may be well worth investing in, particularly for selected internal champions who will be needed to get the project going and give it impetus. One-off training costs are minimal compared to system setup, and they provide solid human foundations on which to build a condition-based maintenance project.
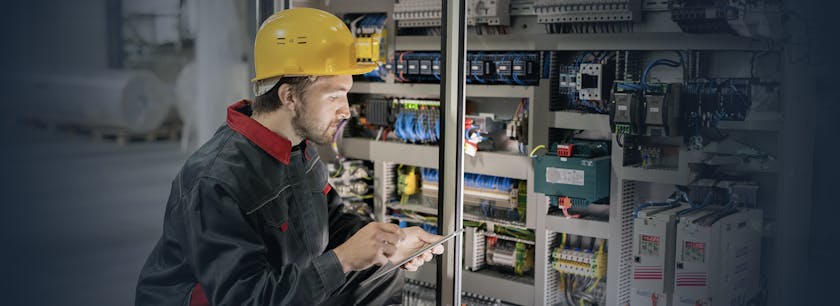
4. Seven steps to successful condition-based maintenance
Creating a successful condition-based maintenance programme with real-time monitoring requires a thought-out structure, starting with understanding what you want to achieve. Here are seven steps that outline the process and allow you to plan for each step in advance.
1. Define your condition-based maintenance project
Determine what you want to achieve with activities such as real-time monitoring and what parts of your operation the project will cover. The critical driver is usually reducing machine downtime, but it is also worth clarifying other objectives, such as maximising machine lifespan, improving product quality, reducing maintenance costs and streamlining workflow for maintenance personnel.
2. Identify your critical equipment for condition-based maintenance
There are items of equipment that are critical to the operation. These should be at the top of the condition-based maintenance list. Other equipment that should be on this list are those that either break down frequently, pose a safety hazard or appear to have unpredictable behaviour. This will form the starting point for your strategy. Condition-based maintenance systems can be scalable – you do not have to do everything from the outset.
3. Choose your sensor technology for condition-based monitoring
All the sensor technologies for condition-based monitoring have advantages and limitations. Choose the machine health monitoring technology that matches the equipment type and is appropriate for the failure mode that the equipment is susceptible to. Typically, temperature, vibration and acoustic sensors have the broadest range of applications, with thermal and oil analysis also common. Other sensors can also be considered for equipment health monitoring.
4. Start setting the standards for condition-based maintenance
Initial baseline data must be collected to establish each monitored machine's normal operating conditions and performance levels. Historical data may not be available at this stage, but if it is, it can start creating the baseline performance of the asset. Other data sources that can help build this baseline are the equipment specifications, operator knowledge and industry standards. All parameters can be changed as the data provides more revealing information, but at this stage, we will also need to define the initial tolerance thresholds used to assess the asset's performance.
5. Collect the data for condition-based maintenance
Select the condition-based maintenance software that will collect all the data for equipment health monitoring from the sensors and then present it in a usable format to the operator. This will be your interface to the system, so make sure you are comfortable with it. There should not be problems but check that all the selected sensors and any other software packages (e.g., ERP and MES) are compatible. This software, typically a CMMS (computerised maintenance management system), is the environment where the user can visualise what is happening in the system. It is also where real-time monitoring alarms can be raised when asset thresholds are crossed and alerts sent to appropriate personnel.
6. Put the information into action to make the most of condition-based maintenance
This is when maintenance strategies can be developed and matured. Remember condition-based maintenance is just a tool for machine health monitoring. At this stage, all the information collected through the condition-based maintenance system can be used to work towards the targets set out at the beginning of the project. Streamline maintenance, decreasing it where possible and increasing it where necessary. Fine-tune the condition-based maintenance strategy to deliver the most cost-effective solution, resulting in the best operating health of your assets. Everyone involved in the workflow should understand their role within the condition-based maintenance programme.
7. Monitor and optimise your condition-based maintenance strategy
The condition-based maintenance system and real-time monitoring techniques should mature over time. Historical data gathered from real-time monitoring will build up, making the system more accurate and a better representation of the characteristics of your assets. Refine the system and learn how machines respond to quicker or delayed maintenance then compare it with pre-condition-based monitoring data. Ask yourself, are maintenance costs and asset failures down? And are machine uptime and productivity improved?
However, implementation of condition-based maintenance does not come without challenge. And there are several factors that must be considered to avoid complexity and risk.
Recognising the challenges of condition-based maintenance
- Keep control of implementation costs. The broad choice of sensors and other specialised equipment means initial projects can quickly become over-engineered, leading to complexity and cost.
- Ensure data collection systems are robust and can be scaled. Real-time diagnostics will be a critical part of the programme, and the software must be able to manage data flows as they increase.
- Do not overlook integration issues. The modern systems that underpin condition-based maintenance must often work in tandem with older equipment, requiring connectors that ensure compatibility.
- Put data security at the heart of deployment. Condition-based maintenance depends on data collection and storage, so the necessary data security and access protocols must be put in place.
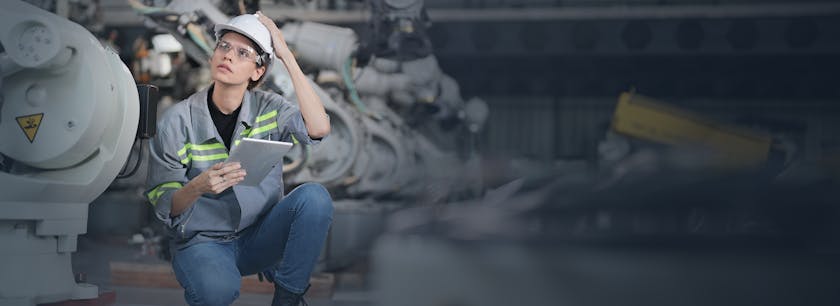
5. Your partner in condition-based maintenance
The application of condition-based maintenance techniques with real-time monitoring can be a game-changing tool but choosing and implementing the right strategy and system is an important factor in its success. A partner like EU Automation can play a pivotal role in ensuring a condition-based maintenance strategy is suitable for an industrial set-up and meets its full potential. Every process and asset is different. Even the same machine in a different setting will have variations resulting from the way it is set up, its age, its previous maintenance history, the way it is being run, the expertise of the engineers, the process fluids involved, the ambient environment – there are endless variations that mean no two applications can ever be the same. Consequently, there is no single off-the-shelf solution.
Interestingly, EU Automation’s heritage comes from supplying reconditioned and obsolete parts. So, while other companies approach condition-based maintenance and real-time monitoring as an out-of-the-box solution, EU Automation has a far deeper understanding of how equipment wears and performs over time and where the failures are most likely to occur. It’s a case of knowing how to wear – and how not to wear.
Technology implementation for techniques such as real-time monitoring works best when the right people drive it. Identifying the right people in your own organisation is half the battle – the other half is the people you partner with. Critical to this is the speed at which EU Automation can source and supply essential and hard-to-find automation and control components, delivered quickly and cost-effectively, anywhere in the world. This service means manufacturers get speedy access to the parts they need to support maintenance activities – reducing downtime and enhancing productivity and profitability.
Partners of EU Automation have a single point of contact, resourceful and responsive individuals who are always prepared to go the extra mile and aim to forge long-term business relationships based on trust. Across a wide range of geographies and languages, EU Automation is working with its partners to reduce downtime and support productivity and profitability. Apart from anything else, EU Automation is a company with thousands of control and automation parts – new and reconditioned - in stock from leading automation suppliers. If your condition-based maintenance and real-time monitoring program reveals replacement parts are required, they will have them ready to dispatch off-the-shelf.
Support is available through many channels, including website, email, live chat or phone, while the company’s ‘follow the sun’ support facility ensures questions are answered quickly and efficiently. So whatever condition-based maintenance and real-time monitoring strategies you pursue, EU Automation can act as a trusted partner.
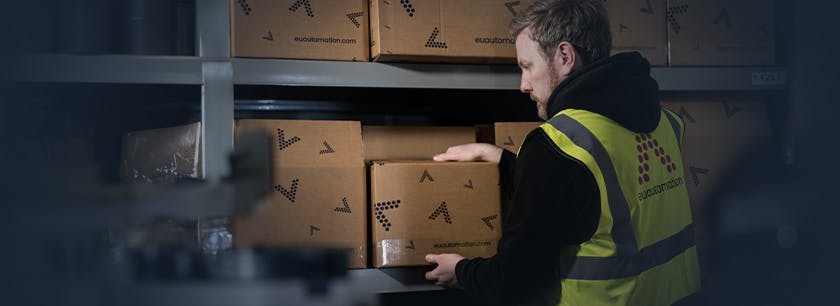
Help and advice for condition-based monitoring
Specialist organisations also exist to provide support with the adoption of techniques such as condition-based monitoring.
The International Society for Condition Monitoring exists to help organisations pursue condition-based monitoring strategies.
The organisation provides a forum for condition-based monitoring – bringing together an international community with the common aim of achieving excellence in the development and practice of condition-based monitoring and related diagnostic technologies.
The society will achieve its aim through:
- Facilitating a worldwide network for the interchange of knowledge on condition-based monitoring
- Encouraging and supporting national and international condition-based monitoring seminars and conferences
- A high-level condition-based monitoring online journal
- Providing input into the development of condition-based monitoring training, qualification and certification programmes
- Contributing to the development of international standards for condition-based monitoring
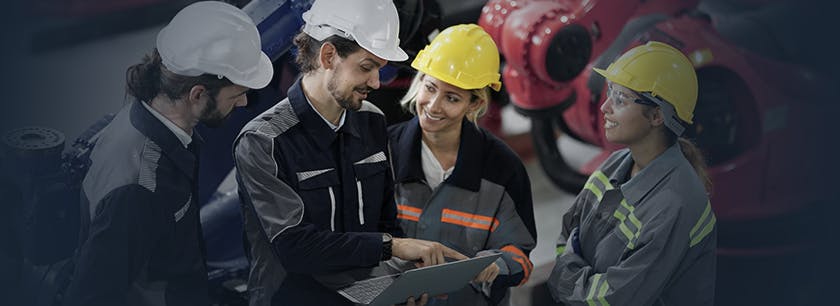
6. What next for condition-based maintenance with real-time monitoring?
The digital transformation of manufacturing characterised by Industry 4.0 and the IIoT uses the twin weapons of technology and human creativity to move the sector to new levels. These are the levels that are demanded by modern society – energy efficiency, environmental impact, personalisation and flexibility, to name a few. Meeting these challenges could not have been done using the manufacturing strategies of the past, but there are technologies in this digital era that enable creative engineers to evolve the industrial sector. And, as always, more technologies are waiting in the wings.
Condition-based maintenance techniques and the real-time monitoring that it allows are both part of and subject to this evolution. While condition-based monitoring presents a data-driven tool for maintenance management, the journey continues beyond there. Healthy machines are productive machines. Increasingly, we will likely see real-time monitoring techniques and data fuse with control and automation to provide further efficiencies. But what are the technologies that will make this evolution possible?
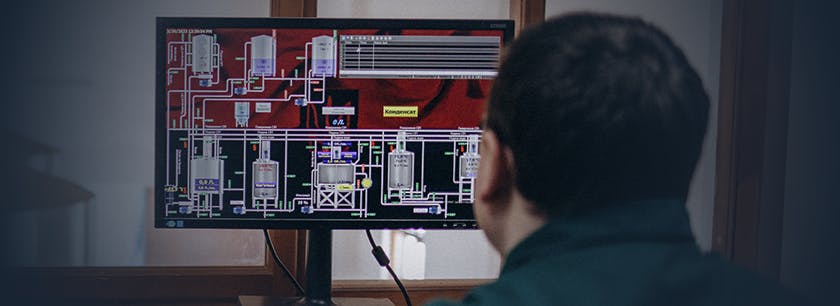
1. IIoT and edge computing.
The global market for industrial automation products will be approximately $115 billion in 2025, according to McKinsey [7], representing compound annual growth of about 3.5% since 2019. While only a small part of this ($6.4 billion) is attributed to automation based on the IIoT and cloud computing platforms, it is a segment forecast to grow around 18% in the same period. The connecting technologies used in automation are the same as those used for machine health monitoring, so the rapidly increasing adoption and development of the IIoT can only support further uptake of condition-based monitoring.
Thanks to the increased processing power of devices, computing at the edge can also make sensors more capable and, importantly, truly provide real-time monitoring without the latency issues that can exist with cloud-based systems.
2. 5G and Wi-Fi 6
The emergence of 5G and Wi-Fi 6 wireless technologies could also substantially impact condition-based monitoring. With less latency, bigger bandwidth and the ability to have more extensive connected networks, the performance of real-time monitoring systems could be significantly boosted.
3. Digital twins
These digital representations of physical things can be used for many purposes. One application is to run simulations of how a system might behave if variations are made, and this can be based on data collected from the real world. It makes sense that the data taken to improve condition-based maintenance performance with real-time monitoring can be tied into the digital twin and used for managing and evolving the factory. The standardisation of condition-based maintenance data based on real-time monitoring is a good fit for the digital twin philosophy. Digital twins are more challenging to create for legacy facilities, but newly designed factories, where the whole design is inherently digital, are more easily reproduced as digital twins from the outset. With the rise of this technology, McKinsey predicts the digital twin market to grow by 35-40% annually through 2030 [5], which could accelerate condition-based monitoring strategies, particularly within new facilities.
4. Artificial Intelligence
AI – and its little sibling, ML – will play a part in all of the technologies above, making all of them more functional, more accessible and ultimately more powerful. Specifically, ML already plays an essential role in real-time monitoring. The more data and the better it is analysed, the more efficient and accurate a system will be. ML can be built into how a condition-based monitoring system works, and improvements in ML algorithms and the data it works with can only make it more robust.
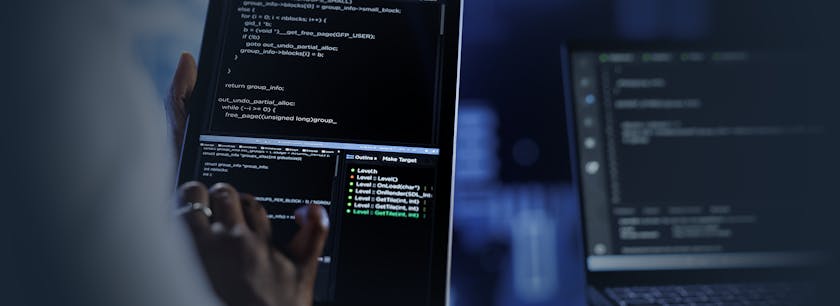
7. Why condition-based maintenance with real-time monitoring makes sense
Committing to a condition-based maintenance strategy with real-time monitoring makes sense for all the reasons given in this guide – the benefits to the process, the staff, the business and ultimately, customers can be considerable. On an individual basis, an asset covered by technologies such as real-time monitoring is likely to run for longer, be more productive and energy efficient, cost less to maintain and be safer for onsite staff. New technologies are being developed that will improve real-time monitoring and condition-based monitoring performance still further – providing even better equipment downtime analysis.
Implementing a condition-based monitoring strategy and real-time monitoring techniques is not an easy journey to take alone. However, there is plenty of help at hand. Condition-based monitoring is a developing technology, but much real-world end-user experience exists. It is a proven methodology, and plenty of users and suppliers can provide evidence of how to build a successful condition-based maintenance strategy.
With expertise in supporting maintenance engineers with its vast stocks of off-the-shelf spares backed by a global sourcing and supply network, EU Automation can add significant value to a company looking to modernise its maintenance strategy. It can be invaluable to understand what the user is trying to achieve, allied to knowledge of equipment and how it behaves over its operating life. But more importantly, ‘change’ is about people. To implement a successful condition-based maintenance strategy based on real-time monitoring, you need the right people, both internally and externally. EU Automation, with its dedicated staff permanently on call, can provide external support to make your condition-based maintenance programme a success.
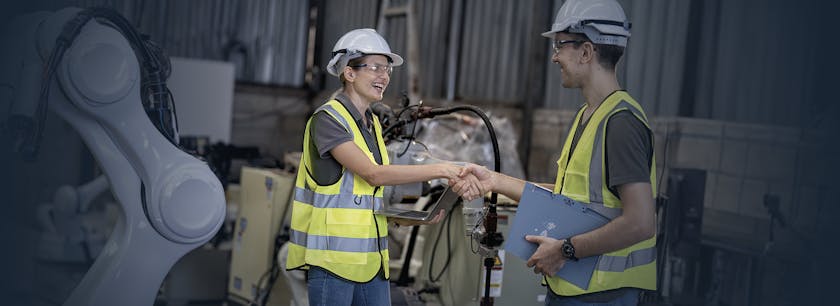
References
[1] Maintenance Costs and Advanced Maintenance Techniques in Manufacturing Machinery: Survey and Analysis, by Douglas Thomas and Brian Weiss - https://www.ncbi.nlm.nih.gov/pmc/articles/PMC9890517/
[2] Statista
[3] https://www.plantengineering.com/articles/plant-engineering-2017-maintenance-study/
[4] https://www.mckinsey.com/capabilities/operations/our-insights/establishing-the-right-analytics-based-maintenance-strategy
[5] Hashemian H. M., Bean W. C. State-of-the-art predictive maintenance techniques. IEEE Transactions on Instrumentation and Measurement. 2011;60(10)3480–3492.
[6] https://new.abb.com/metals/digital/abb-ability-asset-vista-condition-monitoring-for-metals
[7] McKinsey and Company, ‘Is industrial automation headed for a tipping point?’ June 2023
Explorar más sectores
Aquí para inspirarte.
inspirar
inspirar
inspirar
Reciba novedades periódicas e información real sobre automatización directamente en su bandeja de entrada.