How much does an hour of downtime cost you?
2020-03-11
4 min read
Oneserve reports that malfunctioning machinery costs UK manufacturing 3% of all working days, or £31,000 per company each year. The report also states that three-quarters of UK manufacturers outsource equipment maintenance. This means that each business is spending £120,000 a year on average. Lost business and maintenance costs are the most obvious consequences of downtime, but they are not the only ones.
The figures provided by Oneserve are worrying. However, even more concerning are the findings of Aberdeen’s independent research. According to them, 70 per cent of companies lack awareness of when their equipment is due for maintenance. Additionally, 80 percent are unable to calculate how much an hour of downtime is costing their business.
Why do businesses need to learn about the impact of downtime?
However, understanding the true cost of downtime gives businesses a significant competitive advantage. By quantifying the financial impact of outages, businesses can make informed decisions about resource allocation and investment strategies. Instead of relying on intuition or guesswork, businesses can base their decisions on concrete data and analysis. This approach leads to more efficient resource utilization and a more resilient IT infrastructure.
For example, managers could be hesitant to invest £100,000 to save ten minutes of downtime a day. But if we establish that downtime is costing the company £24,000 an hour, those ten minutes are worth £4,000. Therefore, the initial investment will be repaid in only 25 days.
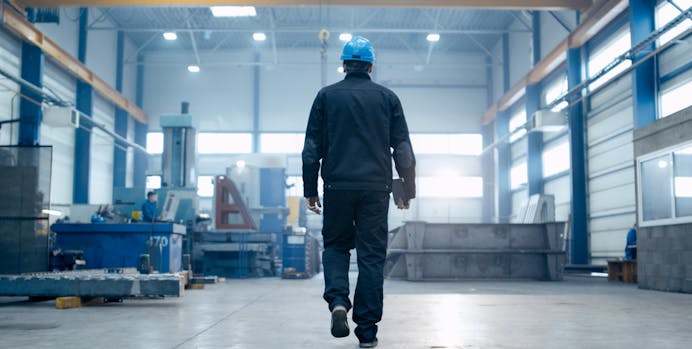
The tangible downtime costs
A business’s true downtime cost (TDC) is the sum of all costs sustained while production is on hold. As well as the resources needed to fix the cause of the problem. These include lost production, fixed costs such as labour and utilities, replacement parts, and maintenance. Also, the impact of downtime can lead to lost businesses opportunities and erosion of clients’ trust.
The true downtime costs can be divided into tangible and hidden costs. Intangible costs, though less readily quantifiable, can have equally significant long-term impacts. Including damaged customer relationships, reputational harm, decreased employee morale, and productivity. Alongside, missed opportunities, and regulatory compliance issues.
Tangible costs represent immediate and direct financial losses. Including the cost of lost production, labor costs, overtime costs, maintenance costs, and customer refunds.
Consider the following: a company regularly produces 500 products per hour and makes a profit of £25 per item. Therefore, they will experience a loss of income of £12,500 for every hour of downtime that the company experiences. Having said that, this is only a surface-level discussion.
Employees’ salaries and utilities are also substantial costs. When equipment goes down, the company produces less while using the same amount of labour and retail space. Sometimes these costs can even rise, as the maintenance team might need to work overtime to get the system up and running again.
Another significant cost, especially for plants working with perishable goods, is that of lost or damaged product. For instance, a milk processing factory will have between twenty-four and forty-eight hours to complete production. This depends on the temperature of the surrounding environment. If the issue is not resolved in a timely manner, the entire quantity of milk will be discarded.
Therefore, firms that handle perishable goods must prioritise downtime prevention measures to protect their inventory and bottom line.
The hidden costs of downtime
Besides the most immediate costs of downtime, there are others that might be difficult to calculate. However, these costs affect a company's performance just as negatively.
The first is the cost of depleted inventories. The stock begins to decline after production is paused for a certain number of hours.
The impact of downtime extends beyond the immediate halt in production. After operations restart, the plant needs to work harder to make up for lost productivity and keep serving clients. This often calls for major adjustments to the production schedule. As well as, increased resource utilization, leading to additional costs and potential risks.
To make up for lost time, the plant may resort to overtime work for employees. Thus, increasing labor expenses and potentially leading to employee fatigue and burnout. Machines and equipment may also be pushed to their full capacity, increasing the risk of breakdowns and maintenance issues. This can place undue strain on the plant's infrastructure and shorten the lifespan of its assets.
The new cost of downtime
The manufacturer incurs a new cost if the plant is unable to compensate and clients are not serviced on time. This is a loss of customers. When downtime impacts clients, they may begin to question your ability to supply goods on time. This means they may also begin to look into working with more reliable suppliers.
Therefore, protecting client relationships and guaranteeing long-term corporate success depend heavily on downtime prevention.
Finally, downtime hinders creativity. There is no energy or money left for innovation when the company's attention is solely focused on maintaining machinery. Or even the resolution of issues that arise during production. This cost can seem negligible at first, but over time it seriously restricts a business’ competitiveness.
Companies that place a high priority on preventing downtime and cultivate an innovative culture will be better able to stay ahead of the curve. To reduce your unplanned downtime today, find your reputable supplier with EU Automation.