- Accueil >
- Industries >
- How to get robotics right >
-
Industry Report
How to get robotics right
Ever wonder why some automation projects succeed while others falter? Getting robotics right can be a game-changer for your manufacturing operation. This guide takes an extensive look at the intricacies involved in automation projects, the common pitfalls you could encounter, and how to avoid them. But most importantly, it serves as a step-by-step roadmap to your successful automation adoption journey. Don't miss this opportunity to leverage the power of automation in your manufacturing process.
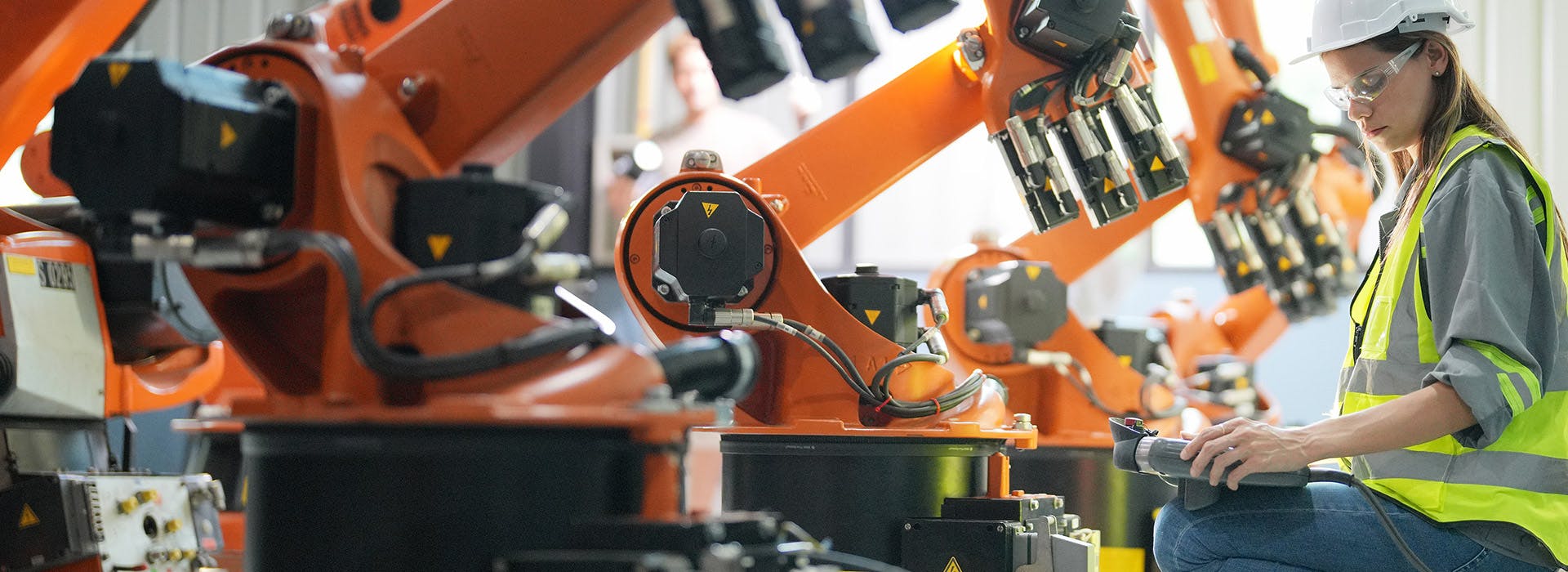
1. Industrial automation comes to the fore
Automation can bring enormous benefits to industrial environments like manufacturing plants. From increased production output and repeatability to improved worker safety and lower operating costs, the automatic operation of specific systems can bring multiple advantages for businesses and employees alike.
Indeed, the global industrial market for automation is expanding fast, having been valued at $207bn in 2022 and is expected to reach $265bn by 2025 [1]. This growth has resulted in the widespread deployment of technologies, such as robotic arms in various verticals, such as automotive, pharmaceuticals, electronics and food and drink. Adoption is being driven by advances in critical supporting technologies such as sensors, pneumatics, machine vision and advanced mechanics – allowing automated systems to become faster, cheaper and more accurate.
Meanwhile, the digitalisation of manufacturing environments – characterised by the emergence of the Industrial Internet of Things – has seen the seamless integration of wireless communication, cloud platforms and big data analytics, providing end-users with real-time information based on historical trends and patterns.
Engineers can benefit from hitherto unseen insight into automated systems' performance in such environments. Future factories will deploy AI-based systems to deliver exciting concepts, such as self-correcting machines that can adapt to maintain performance and efficiency.
In short, automation is changing the face of the manufacturing environment – making it smarter and more fit for the future.
Robotics and automation on the shop floor
But how exactly does this performance enhancement translate on the shop floor in the real world? For robotics, specifically, improved subsystem capability has improved accuracy, payload, flexibility and reach, leading to deployment in an ever-increasing number of end-user applications. Robots have pushed further and deeper into manufacturing activities, from picking and placing to assembly, welding, painting, testing and other hazardous tasks.
For example, powerful robotic arms are now commonly used in demanding activities such as deburring and polishing engine blocks in the automotive sector. This process requires a combination of force, precision and speed. Meanwhile, a new generation of collaborative robots designed to interact directly with humans and perform tasks in cooperation with them has supported a host of more complex and delicate operations. These collaborative robots often perform repetitive tasks, such as attaching door handles or windshield wipers or installing car seats, which humans historically would have carried out.
Meanwhile, in other sectors such as food and beverages, advances in technologies such as machine vision mean robots can now be used to spot minor blemishes or deviations in the shape of produce set for human consumption – before picking arms remove them from the process line. Robots are also deployed for packaging and palletising, being configured to have the strength to lift heavy loads while treating them delicately enough not to cause any damage.
Robots are ubiquitous across the industrial sector. And as concepts such as AI-based systems and machine learning continue to improve robotics accuracy, so their technical capability and application looks set to increase.
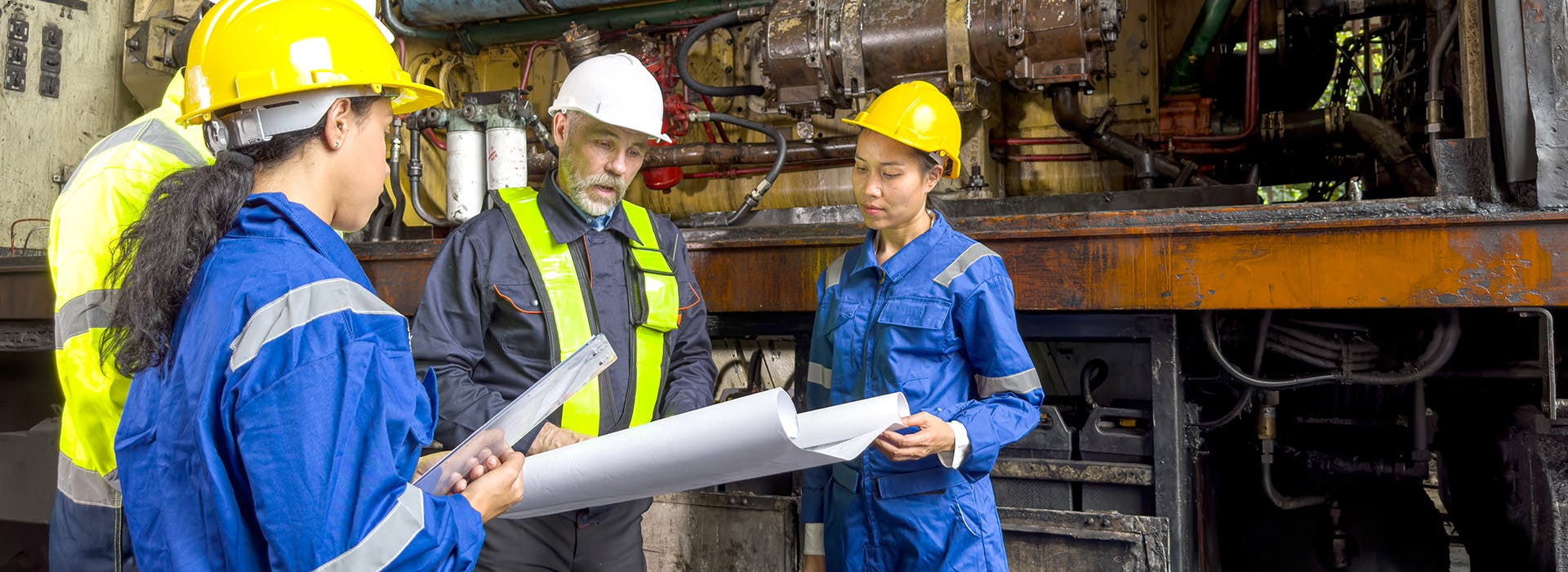
2. Recognising project complexity
Having established that automation adoption can deliver significant operational value across industrial environments, it is essential to acknowledge that such positive outcomes are only made possible when adoption is carried out well. This process requires multiple decisions and actions to be organised and structured, encompassing the complete project preparation, implementation, operation and maintenance lifecycle. Done correctly, engineers involved in adopting automation can help their company realise powerful benefits in efficiency, output, accuracy and flexibility. But sadly, that is not always the case.
In honesty, automation adoption is a complex and multi-faceted affair. It often involves a lot of stakeholders from different disciplines inside an organisation, with varying levels of technical knowledge and skills. It requires sound decision-making and good communication to reach a desired set of objectives. Done incorrectly, though, any automation project can be doomed from the start. Common mistakes often include poor product selection, a lack of joined-up thinking between engineering and IT staff, failure to devote enough time for deployment, inadequate integration and testing and ineffective monitoring and maintenance. In truth, the potential pitfalls of automation are numerous in scope and costly in outcome – and for the engineer responsible for the project, they can damage a career.
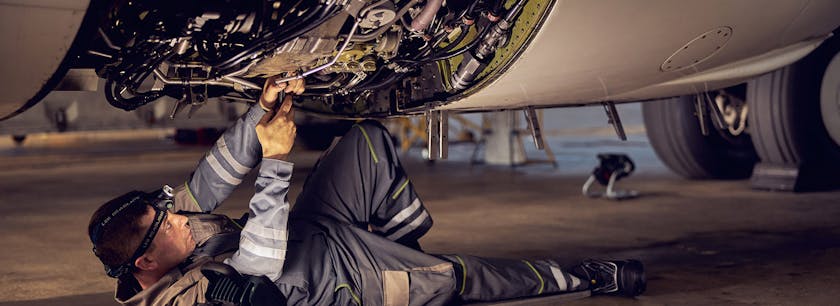
The pitfalls of automation
So, where has automation failed to deliver on its promises in manufacturing settings and what have been the ramifications? In recent years, there have been several high-profile examples of companies and engineers getting things badly wrong – and it can happen at blue-chip organisations with considerable resources and teams.
A couple of years ago, commercial aircraft manufacturer Boeing had to rethink its production strategy after facing problems with the performance of an automated system to drill holes and install fasteners in the forward and rear sections of fuselages for a new commercial airliner [2]. The system, which held large, curved panels in a cradle while moving robots performed various tasks, reportedly suffered from long set-up periods and poor accuracy. It was eventually replaced with a more straightforward system and traditional human machinists. [3]
Meanwhile, electric carmaker Tesla suffered bottlenecks in Model 3 sedan production in the automotive sector when overly complex automated systems slowed down throughput to such an extent that the company struggled to meet targets. [4] Chief executive officer Elon Musk admitted that the company deployed too many robots, with a "crazy, complex network of conveyor belts – and it was not working".
As with many others, the automation failures in these high-profile examples will have occurred for multiple interlinked reasons. Whether designing a project around a task or process instead of the people it will support, not developing a good plan or having unrealistic expectations, automation adoption can go wrong at any time. That is why it requires a structured, thoughtful and systematic approach that provides the best chance of success.

Using this guide to get automation adoption right
To get to that desired endgame, engineers need a plan. And that starts with the listing, evaluating and implementing a core set of processes and activities for any automation adoption project based on four key areas - project preparation, implementation, operation, and maintenance. One set of outcomes will inform another. But by breaking them down into four identifiable segments, it is easier to set an over-arching vision for an automation project based upon a definitive and comprehensive set of actions.
But where to start? That is where this guide comes in. The document provides a best-practice template for getting robotics right - including a checklist for benchmark actions in project preparation, implementation, operation and maintenance. It also offers advice on what not to do, with common mistakes and pitfalls to avoid featured at the end of each section.
Every organisation is different, so the approach to getting robotics right will differ slightly each time. But the guide aims to offer a framework of practical advice that can be applied to the unique circumstances of individual companies - enabling automation engineers to deliver powerful benefits in efficiency, output, accuracy and flexibility, whatever the application.
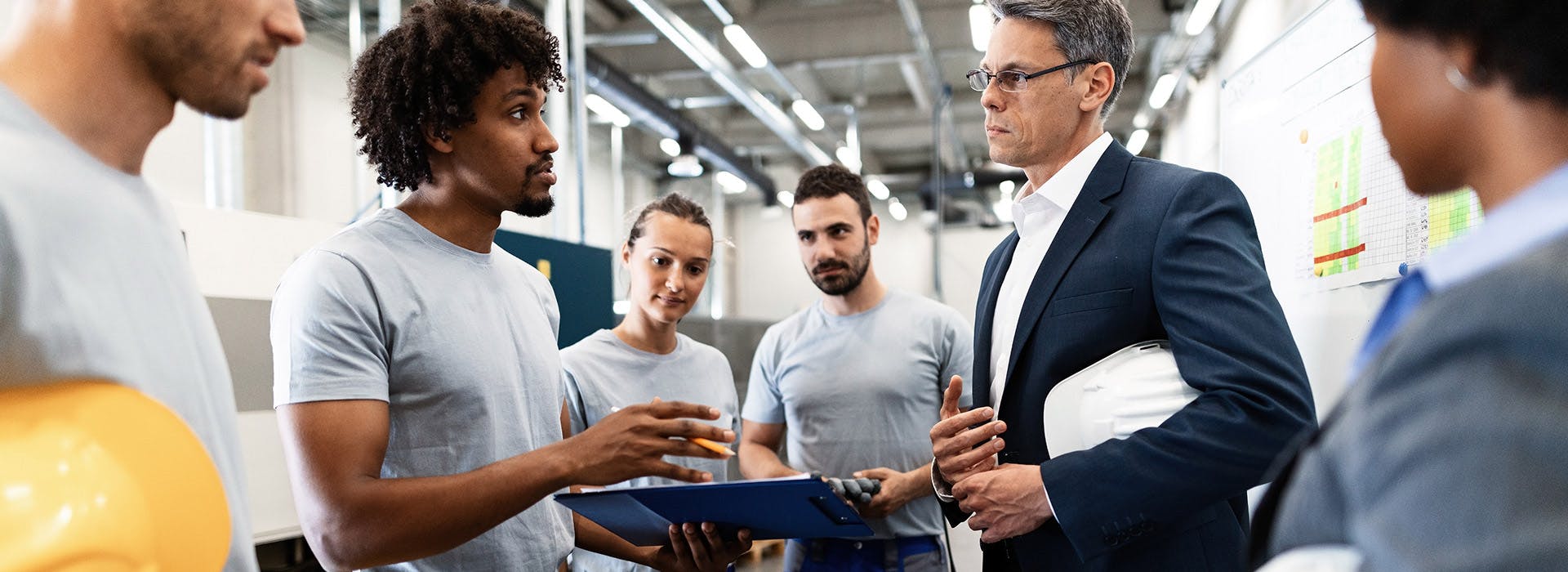
3. Project preparation
Nearly all successful technical projects are underpinned by detailed project preparation. While a comprehensive plan does not always guarantee success, it increases the chances of the project meeting its goals and remaining on budget. The initial preparation phase provides a necessary foundation and establishing targetable objectives will ensure the venture starts on the right path. Failure to define clear goals will leave the endeavour open to missing budget and time constraints or providing no tangible benefits.
While the importance of planning is true for any business endeavour, its significance is multiplied in automation projects where the associated costs of robotics, and the complexity of balancing human and machine resources, make it incredibly challenging to integrate new systems with existing processes harmoniously. A well-produced plan should have a clear target while covering time/budget scales, procurement procedures and strategies for implementing, operating and maintaining the equipment.
Use a project planning method
When preparing for an industrial automation and robotics project, there is a wide range of planning methods available, such as Kanban, critical path method (CPM), critical chain project management (CCPM), Scrum, new product introduction (NPI) and Agile. These all have strengths and shortcomings, and selecting the correct technique for your next automation project will be based on several factors.
The first factor for many projects is company policy. Large technical organisations typically have a dedicated planning framework, including a preferred method or recommended software to support the process. For companies without a set procedure, selecting a plan depends on the type of robotics, resources available, project complexity, potential risk, business structure and end goal. By scrutinising these elements, you can more precisely choose an accompanying planning method, but regardless of the technique selected, there are several essential aspects to any project's success.
Set a measurable target
One of the most common mistakes in automation projects is to lose sight of the primary objective. This oversight can occur for several reasons, such as trying to achieve too much in one project or setting a heavily subjective target. For example, a typical project could have a primary goal of 'increasing assembly line output,' and while this is a potential target, it needs to be measurable. Instead, through a detailed analysis of the current process, we can determine critical benchmarks such as the total output, running costs, potential wastage and maintenance time. We can produce a quantifiable goal from here, such as 'increasing output by 15% while reducing annual maintenance costs by at least 10%'. This target is both measurable and details the benefits, providing a simple statement that sets the outline for the entire project.
Establishing a tangible goal gives you a consistent standard to aim for – this is essential in internal conversations and when choosing suppliers. Implementing greater automation can often be disruptive and contentious; by presenting quantifiable benefits, the endeavour is far more likely to receive the necessary support from colleagues. This benefit applies to procurement as well. If you are exploring using a SCARA robot to replace a repetitive manual process, challenge your suppliers to quantify any improvements – how will this increase output? What reduction in downtime will you see? What is the return on investment? Leading manufacturers will have the data and real-world examples to assist with your venture, so use their expertise to your benefit.
Although it is tempting not to have definite targets as it can create accountability, an effectively run project should always quantify the projected outcome. When starting a sizeable technical endeavour, the first primary task is to define a target, providing you with a clear outline for the rest of the planning and implementation tasks.
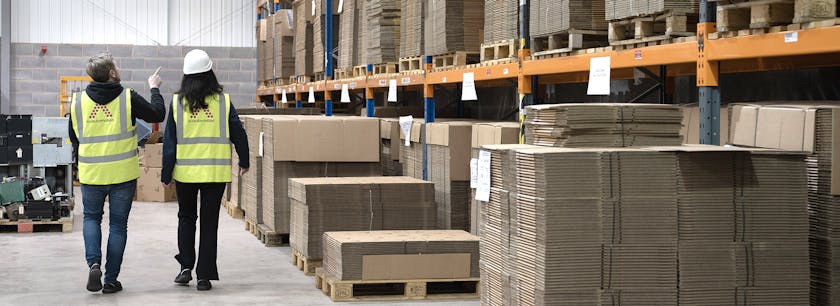
Produce detailed research specific to your operation
Once you have produced a detailed target statement, the next step is to research the relevant factors within your company and industry that might affect the project. A costly mistake that has affected numerous large-scale projects is to lose the focus of the current business, whether this is its own manufacturing process or its position in the market. A famous example of this was HP's efforts to copy the success of the Apple iPad with the HP TouchPad. The costs of creating a new manufacturing process just for this product and the subsequent software development contributed to a substantial loss of $3.3 billion for HP in 2011. This failure, in turn, jeopardised the stability of HP's successful core computer and laptop manufacturing operations for the next few years. While it is important to follow developments within the market, you need to ensure that the provided solutions can be implemented within your company. Just because a specific robotic installation or automation process succeeded for another company does not mean it will work for you.
When implementing a new automation process, it is essential to identify areas where it will harmoniously add value and improve efficiency for your specific operation. While new robotics might bring an increased output and work elsewhere, if the costs to implement the setup within the confines of your business are too high, the project should be stopped.
The first step of any research is to analyse your current situation, whether this is an ageing assembly plant, a state-of-the-art laboratory, or a sizeable packaging facility. Within this assessment, you need to identify where robotics can improve the output or reduce the overall running cost of your business. A typical upgrade example is to identify repetitive tasks within your overall operation – the greatest strength of modern robotics is its ability to undertake many repetitive tasks at incredible efficiency. This speed gain provides a logical area to implement a robotics project.
A second approach is to target bottlenecks. It is possible to identify inefficient individual tasks within a more extensive process through detailed analysis, or often from communicating with individuals who operate within the process. These tasks are ideal for deploying additional or new automation products, provided the physical operation is suitable for robotics. Increasing the efficiency of the task to match the proceeding operations closer will ease the bottleneck, improving the system's total output.
Once you have identified a potential upgrade and its reasoning, the budgetary impact and efficiency increase need to be determined. Through detailed financial and process analysis, you can use these factors to determine if the cost of an automation upgrade is justifiable. Any business venture which takes too long to provide sufficient return on its investment should be halted at the planning stage.
Produce a plan and create contingencies
With a clear goal and detailed research backing the feasibility, the next stage is to produce a detailed plan. This process involves setting achievable timelines for each step and identifying budgets and resource requirements. A common mistake when constructing a plan is to be lacking in detail. Creating a plan that tracks to individual hours instead of days, that accounts for every single cost down to the smallest bolt and specifies all personnel required, will produce a clearer road to success. The accumulative nature of both time and finances also means that continuous minor inaccuracies within a plan can have a substantial combined effect by the end of the project. A comprehensive plan must accurately cover the complete planning, implementation, training, operation and maintenance phases.
Once a plan is in place, the various stakeholders should assess the potential risks and develop contingency strategies. Examples of risk and countermeasure include labour uncertainty, such as a key person on leave. We can mitigate this risk by using two individuals for the task or by shifting the plan's timeline. Risks can cover factors such as regulation change, funding alteration, critical components missing deliveries, deadlines being ignored, or third parties not meeting targets. In each case, produce a list of potential scenarios specific to your project and create actionable strategies that will help to reduce the impact. The more contingency plans made, the greater the chance of success.
Involve all key stakeholders
While the phrase 'too many cooks spoil the broth' can often ring true, a common mistake in automation adoption is needing to involve more relevant individuals. In their 'Ten Reasons People Resist Change' article [5], the Harvard Business Review highlighted both loss of control and surprising individuals as crucial factors. Continuous involvement of stakeholders, such as IT teams, operators, maintenance personnel and facility managers, helps individuals maintain input. While regular team briefings prevent any surprises which could weaken morale or even stop the venture altogether.
Enhanced cooperation with a more significant engagement of key individuals allows for a greater circulation of information, reducing the likelihood of conflicting timetables or vital information being missed.
Five common planning mistakes
- No planning method – Ensure your project is underpinned with a proven (and suitable) planning method such as Kanban, CPM, CCPM, Scrum, NPI or Agile. A robust and well-matched planning method keeps the project on task and easy to follow.
- Subjective target – A high-quality target must be quantifiable and can be benchmarked against existing numbers. This approach helps the venture gain support and remain on track.
- Poor business integration – While a specific robotics upgrade might work well for one business, that does not guarantee it will work for yours. Ensure the automation will work specifically for your operation to maximise the impact.
- No contingencies – Be sure to plan for every outcome. Use your research to identify potential risks to the project and use critical individuals to create actionable contingency plans, helping to reduce the impact of any potential risk.
- Missing stakeholders – Ensuring all key stakeholders involved in your project increases the overall effectiveness. Individuals should be consulted and kept up to date, helping to make people more positive towards the incoming automation changes.
”
When preparing for a robotics project, there is a wide range of planning methods available, such as Kanban, critical path method, critical chain project management, Scrum, new product introduction and Agile.
”
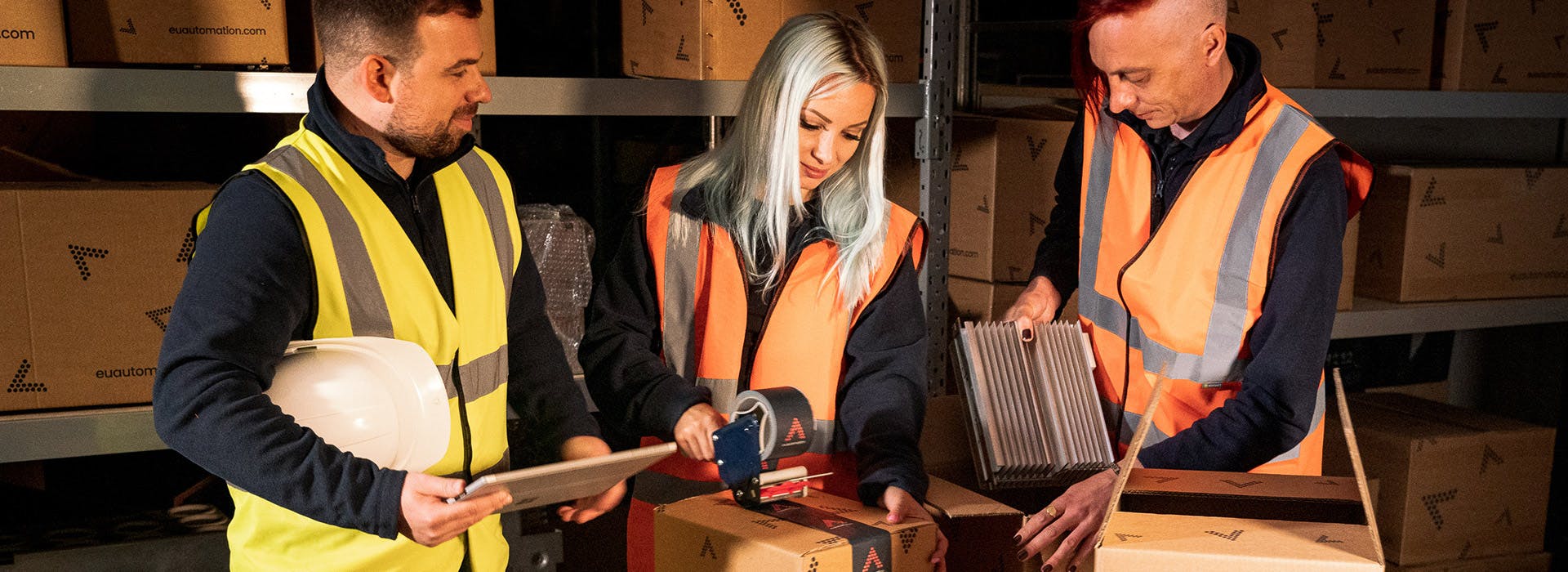
4. Project implementation
Having built a comprehensive plan, the implementation phase is the next step in any automation project. As the most significant project section, it is the biggest opportunity for mistakes to arise. The endeavour's ultimate success will largely be determined by its ability to generate positive change on time while staying within budget and keeping personnel from various departments working harmoniously.
Select the correct supplier
Automation is everywhere, from manufacturing aerospace components to packaging plants. The variety of uses of a single robotic device can be vast, while the industry has nearly endless coverage. When selecting suppliers for your project, the choices can be equally limitless. Picking an incorrect supplier can have a sizeable impact, so how do you narrow the choice?
As observed in the planning phase, robotics excels at replacing repetitive manual tasks, but implementing automation can also be done for various other reasons. Robotics can deliver increased safety, higher precision, greater payloads and the ability to perform multiple complex operations quickly. When choosing the right supplier for a project, there are many factors to consider, but above all is establishing your specific application and core business sector. Combining this information helps narrow your search by highlighting vendors with complimentary values. Leveraging the experience of a supplier who has already supported applications within your industry will allow you to build on their previous success.
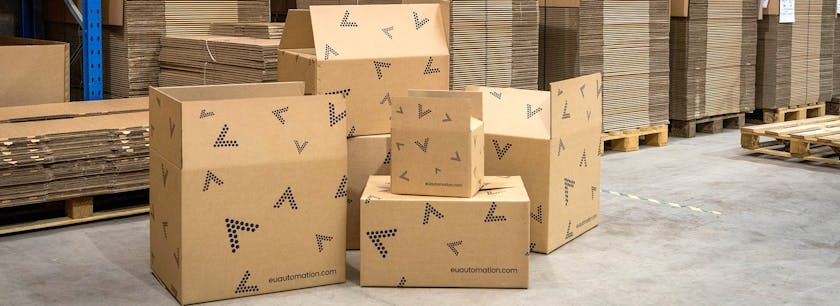
Once you have a shortlist of suppliers, five further considerations will narrow your choice:
- Quality and reliability – Do the suppliers have a proven track record, or are they relatively unknown? Is there an established relationship? For large robotics projects, selecting a vendor that provides a high-quality and reliable service will not just aid the initial implementation but also future maintenance.
- Communication – Automation projects are inherently complicated, but having a responsive and knowledgeable supplier on board can help you avoid costly mistakes. Before placing orders, assess the supplier's communication to determine what level of support they offer specific to your application.
- Value for money – When choosing a supplier, they must represent fair value, not just in terms of the component or assembly delivered, but also their support and after-sales. As with all procurement, be wary of suppliers over-promising or those who are inexpensive.
- Location/geographical reach – All automation projects have extended periods of implementation, operation and maintenance. Having a vendor within a closer geographical region increases their ability to provide on-site technical support quickly. A supplier with an extensive business network can also supply components to your locations more swiftly and efficiently.
- Speed – Lead times for complex robotics can be considerable (a factor accentuated by various global technology shortages). You should check lead times frequently, and if a supplier cannot meet your deadlines, you must not select them. To help increase project success, line up alternative vendors for key systems and, where possible, examine their stock levels for critical spare parts to guarantee your system remains functional.
Determine compatibility with current systems
With the wide range of automation on offer, selecting a device that integrates with your existing systems is critical and often overlooked. The first factor to consider is what level of robotics to implement. Whether this is a fixed automation (such as an automated assembly line), a programmable automation (such as CNC machines and logic controllers) or a flexible solution (such as robotic arms and human assistive robotics).
The magnitude of automation will strongly weigh on how it integrates into your business. Larger fixed automation can take the configuration of a complete assembly line, so you may be replacing an entire facility. At the other end of the scale, smaller flexible implementations (such as a robotic arm) might have to communicate seamlessly with other independent robotics to form part of a combined system. Both examples will have vastly different considerations regarding integration and its effect on operational processes.
When selecting new equipment, neglecting existing systems is often a common mistake. When choosing a solution, first assess the current setup to determine if any devices (such as other robotics, sensors, logic controllers and data loggers) require integration. From here, decide which communication protocols existing systems use and assess this against any new devices to ensure compatibility. If native communication is not possible, you may need to use an intermediate device to 'translate' the protocols between devices, increasing the implementation costs.
Other essential considerations include the device's size, power requirements, operation speed and payload. A more in-depth analysis is necessary to evaluate how new robotics fit into an existing system's day-to-day operation. This will cover factors such as verifying if the maintenance cycle is compatible with existing timings and that the device operates similarly to existing equipment (as this can aid staff training).
Perform comprehensive testing and validation
For heavily regulated sectors such as pharmaceutical manufacturers, thorough testing and validation of robotics equipment is a requirement, with set procedures detailing how to implement new machinery. But this is not the case for many industries, and a lack of framework can permit errors, reducing confidence in new equipment.
As a starting point, checking if your industry or organisation has a framework to follow is advisable. If there is not one available, the short guide below will assist.
- Offline testing – Before installing the equipment, you should perform extensive tests away from the final implementation. Produce a detailed test plan to benchmark efficiency, communication stability and other key performance indicators (KPI), ensuring human tasks are isolated from the tests. This phase aims to thoroughly examine the equipment's performance compared to the original equipment without disrupting the existing process. The testing will display the new device's improved performance while allowing engineers to familiarise themselves with its operation.
Documentation requirement! At this point, you should produce initial training documents to guide operation and troubleshooting. - Final collaboration – Once initial testing and an understanding of the device are attained, involve the relevant stakeholders in a final testing and pre-installation assessment. Sharing new equipment too early can cause people to doubt its operation while displaying it too late can reduce project foresight and potentially cause friction between departments. The perfect time to involve wider stakeholders is after the testing phase, where you can demo the equipment, having ironed out initial problems during testing. From here, as a team, you should produce contingency measures for any potential disruptions that might occur during installation and provide all relevant personnel with a schedule for the installation.
Documentation requirement! Produce detailed installation, operation and maintenance procedures using information from the manufacturer, the testing phase and collaboration with key staff. - Installation and validation – Observing agreed timescales to install the new equipment using the combined efforts of all key personnel. Once installed, through further testing, verify that the device meets the operational and safety guidelines, as well as any relevant industry standards. You should perform a final benchmark to validate that the device is providing the desired improvement.
Documentation requirement! Produce finalised training documents using information specific to the real-world installation. In addition, create maintenance and calibration procedures/timelines. You should collate all documentation and distribute it to relevant parties. - Training – Using the previously created training plan, educate relevant staff on the device's operation, troubleshooting and maintenance. Whether you deliver the training to senior personnel and for them to pass it down through a group workshop or as one-to-one sessions will depend on the automation type and your organisation. At this stage, you must provide all appropriate personnel with the information they needed to undertake their job safely and effectively.
Documentation requirement! Final adjustments can be made to the documentation based on feedback from the training. Provide staff with resources to reinforce any training sessions.
Keep to the plan
During the implementation phase, you must follow the project plan. If shifts occur, they should be justifiable and communicated to everyone involved. A common mistake in many robotics projects is to start with a thorough plan and deviate gradually from it with no traceability. While sticking to and updating a comprehensive plan can take time, it will help to create a professional, quantifiable project with an increased likelihood of success. Suppose significant changes occur or you miss a target. In that case, a detailed plan can help you comprehend what happened, allowing you to benefit from the mistake and positively affect future endeavours.
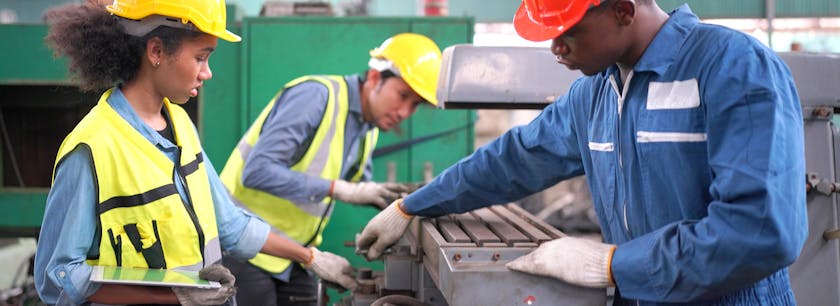
Automation adoption gone wrong
In 2016, the Mercedes-Benz group made headlines when they removed assembly line robots from their Sindelfingen plant while struggling to keep up with the growing vehicle customisation options. The original fully automated robots were replaced with skilled workers equipped with an array of smaller and lighter smaller robotics. Speaking at the time [6], Markus Schaefer, Mercedes' then head of production, stated: "We're moving away from trying to maximise automation with people taking a bigger part in industrial processes again. We need to be flexible. The variety is too much to take on for the machines. They can't work with all the different options and keep pace with changes."
In a similar development, Toyota has phased robotics out of key production areas. The concept is that by employing trained personnel to fulfil intricate tasks (such as forging crankshafts), Toyota can more accurately pinpoint areas for improvement. Discussing the initiative with Bloomberg [7], Mitsuru Kawai (now an Executive Fellow at Toyota) commented, "We cannot simply depend on the machines that only repeat the same task over and over again. To be the master of the machine, you have to have the knowledge and the skills to teach the machine."
Both cases emphasise how we must deliberate the implementation of robotics. Opting for a fully automated fixed automation is excellent for mass production, but it does lack flexibility compared to smaller hybrid human and robotics operations. Similarly, using automation to reduce the skill set of your workforce can create significant problems because of a need for more process insight. Regardless of your automation project, it is essential that the final implementation is harmonious and brings tangible benefits.
”
When choosing a solution, first assess the current setup to determine if any devices (such as other robotics, sensors, logic controllers and data loggers) require integration.
”
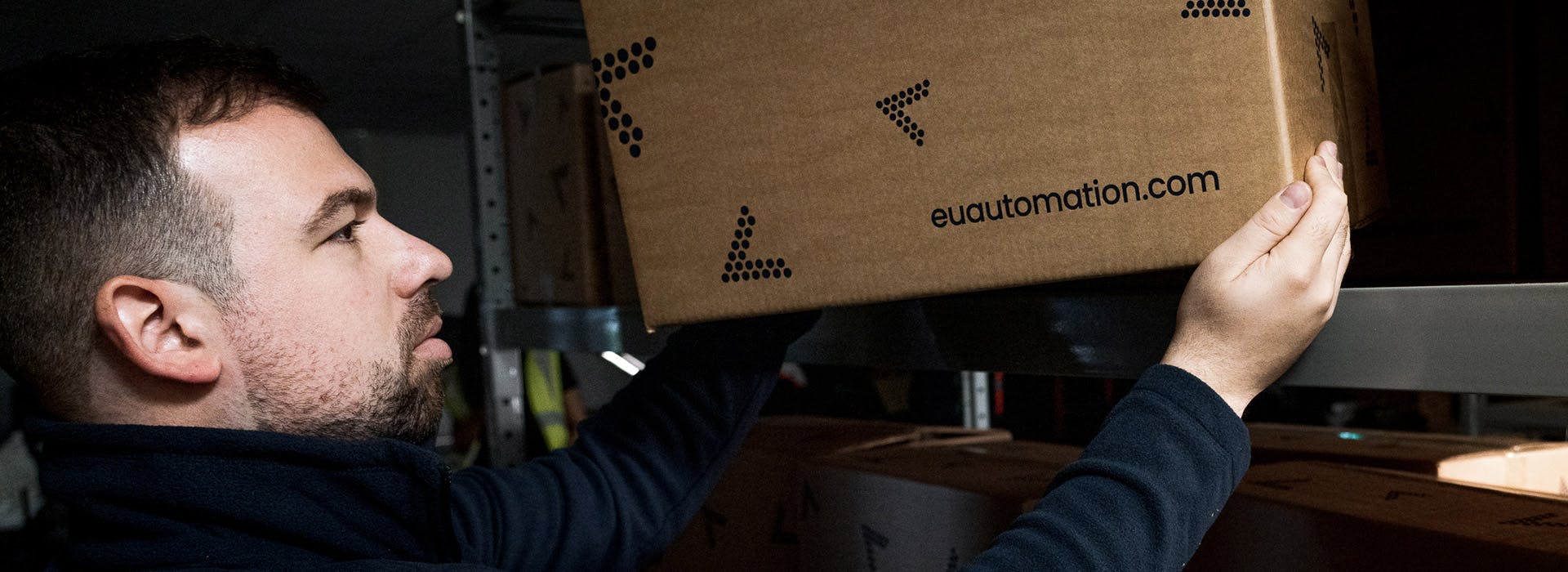
5. Project operation
With new equipment installed and initial training completed, it would be easy to assume the project is nearing its end, but for any comprehensive automation venture, the subsequent two phases are critical for guaranteeing lasting success. Through continued analysis and refinement of operation, your project can ensure optimal efficiency and equipment longevity.
Managing operation procedures
Working procedures and protocols can take many forms, from in-depth user manuals to visual guides displayed next to the equipment. Regardless of the medium, ensuring protocols are up to date and reflective of the current real-world operation is critical. While procedures will have been established during the project's implementation phase, a common mistake is to assume they are static and do not require further input. This assumption might be valid in some rare cases, but in most instances, further honing is needed once the equipment is in place.
For working procedures, an optimal starting point is first to observe how the automation is currently operating and compare this against your initial protocols. These are some of the key elements to assess:
- Operation stages – Are the individual stages of the overall process identical? This will likely be true for fully automated systems, but there may be subtle changes to the running order for smaller automation functioning alongside humans. This could relate to when new material is loaded or for multi-function CNC machine alterations to the order of machining.
- Maintenance intervals – Minor maintenance actions (such as cleaning) might be required more regularly, or manufacturing engineers might feel the initial procedure has intervals too often. Major maintenance is typically determined by the original equipment manufacturer (OEM) and, therefore, should not be modified.
- System integration – Evaluate how the new robotics have integrated within your existing infrastructure. Check that communication and data handling match the initial procedures and verify that physical operations between the new machinery and existing devices (and humans) are identical. For example, operators may remove an individual task from a previous workstation in a multi-process production facility and move it to the new automation as it processes it faster. Equally, if robotics alleviated a bottleneck in production, products may now back up in another area of the facility, creating an additional storage demand.
- Employee understanding – Are all staff members operating in line with protocols and displaying a clear understanding? Observing the process should allow the identification of areas where personnel need further training or perhaps where working procedures lack clarity.
For any identified alterations, communicate with those at the centre of the change to fully understand the reasoning behind the action. Quantitative comparison of the new process against the original should help to identify differences in efficiency, while assessment from health and safety representatives should ensure that no unacceptable risks occur. Through detailed evaluation, determine if the change is positive or negative. Positive modifications should be rolled into updated procedures, with the information redistributed to staff. For negative changes, such as staff circumnavigating safety protocols to speed up processes, senior supervisors should re-communicate the original protocols and their importance.
Regardless of the adjustment impact, you must take suitable action to ensure all staff work efficiently and safely. Failure to do so will jeopardise the project outcome and put personnel at risk.
Monitor performance and track KPIs
Harnessing real-world data is a powerful way to show a project's success and provide a platform for future improvements. With complex robotic systems, establishing what elements to analyse can be difficult. But by utilising key performance indicators (KPIs), you can quickly and accurately track progress and identify improvement areas.
Key performance indicators are metrics that measure the process's success. KPIs always align closely with your project goal, so select metrics which validate the overall target statement. If we look at the example set earlier:
”
Increasing assembly line output by 15%, while reducing annual maintenance costs by at least 10%
”
The metrics we need to confirm we have accomplished this statement relate to the output and maintenance costs. A typical approach would be to monitor the total output of the assembly line against the previous system to determine whether an increase of 15% has occurred.
While this approach can work, you need to know how data can be misleading when evaluating complex automation systems. For example, when producing gas turbine engines, the final product combines thousands of components and individual manufacturing processes. Suppose we have deployed new robotics to assemble the engine nacelle faster, and there is a shortage of fuel control circuits because of a global lack of semiconductors. In that case, the total facility output will reduce compared to our original benchmark, impacting the appearance of the project's success. In these instances, it is essential also to track metrics which are direct measurements of the new automation only. For this example, we could highlight just the time taken to assemble the nacelle around the engine core. This information would show that the facility's current drop in output has occurred elsewhere. Once supply levels for the fuel control circuits are restored, the project's success will visibly affect the total output.
Example KPIs:
To help guide your next robotics project, here is a list of useful KPIs that apply to many automation scenarios:
- Production schedule attainment – This calculated number shows how close the system is to achieving the projected output.
Formula: (actual output / projected output) x 100 - Scrap value – This can be defined as a quantity, time, cost, or percentage (total scrap / total output) and indicates the level of wastage. The choice of a unit must remain consistent when running comparisons.
- Total cycle time – This is simply how long a process takes.
Formula: (cycle end time – cycle start time) - System changeover time – This KPI indicates how much time is lost changing between tasks in larger processes. Provided the available time remains consistent, it can also show a reduction in production time.
Formula: (net available time – actual production time - Throughput (output) – A core robotics KPI, this shows the output capabilities of an automated process.
Formula: (number of units produced / unit of time (day, week, or month) - System availability – This number allows for an easy comparison of system uptime while considering any downtime.
Formula: uptime / (uptime/downtime) - Percentage planned maintenance – This ratio evaluates planned maintenance against emergency maintenance. It is a helpful indicator of reliability and highlights areas ideal for preventative maintenance.
Formula: (number of planned maintenance hours x 100) / total number of maintenance hours) - Manufacturing or maintenance cost per unit – Two core KPIs, these show the cost of the equipment (running or maintenance) per unit produced or cycle completed.
Formula: (total manufacturing cost/number of units/cycles) or (total maintenance cost/number of units/cycles)
Create actionable feedback loops
Four-stage feedback loops are heavily utilised in customer experience industries, where they continually refine the products on offer. Using a similar approach in your robotics project ensures that any initial success continues through a constant cycle of feedback, analysis, testing and review. Below is a typical framework for a four-stage feedback loop applied to a new automation installation. Following it will increase team collaboration, encourage stakeholders to stay involved and help implement change quickly.
Step 1 – Capture feedback
As part of the ongoing equipment operation, you should continually receive feedback from both stakeholders' subjective opinions and quantifiable metrics and KPIs. Real-world performance data is gained from KPI tracking and monitoring metrics. This action should cover efficiency, running costs, communication performance, maintenance metrics and any wastage/downtime.
Key personnel's opinions are captured through conservations, formal meetings, management software and response forms. Defining a single designated feedback method to help manage replies in a medium that works for you may be beneficial. The responses should cover areas for improvement, reoccurring issues, positive factors, integration considerations and ideas for further implementation/automation developments.
Step 2 – Analyse the data
After a suitable time period has passed and sufficient information is collected, analyse the data to ensure it is all relevant and reliable. Carrying only the high-quality facts forward, perform a review with key stakeholders, looking for patterns such as recurring comments or metrics that show room for growth. These issues should be used to create actionable solutions, such as altering the automation process, increasing staff training, or updating documentation.
Step 3 – Apply feedback
All relevant stakeholders should apply the actions created in step 2 harmoniously. For many new optimisations, you may have to perform back-to-back testing against the previous processes – capturing data to validate the changes before final approval. Extensive procedural modifications can take several months to fully validate, while smaller robotic optimisations can be verified in significantly less time.
Step 4 – Follow up feedback
After implementing any actions, the last step is to follow up with further feedback. For actions raised by individuals, this involves confirming with them that the change implemented matches expectations and covers the area for growth. For any activities created through data analysis, additional metrics evaluation is required to confirm the modification is successful and not creating new issues elsewhere.
Doing things right: Five operation management tips
- Market your success – Continually involve staff in the ongoing operation of any new robotics. If the project is meeting or exceeding expectations, invite key individuals to view the system and provide them with any useful resources. This will keep support for your project while helping colleagues with their future robotics ventures.
- Capture sufficient information – It is considerably easier to rule out irrelevant information than to interpret data that does not exist. Always capture as much information as possible, whether this is through data loggers or feedback forms. This is especially true when tracking KPIs in large automation systems.
- Embrace feedback – Receiving feedback is not always enjoyable, but by installing feedback loops into a project, you provide an efficient pathway for improvement that exists on your terms. If you prefer written forms for feedback, create templates and make them readily available.
- Maintain procedures – While working practices should be altered when required, no person or team should work outside of a procedure for a sustained period. Ensuring procedures are updated, and staff are following them ensures reliable operation, maintains safety and increases efficiency.
- Reinforce training – Training should be strengthened with suitable documentation and resources. The best automation projects value continuous improvement, and regular training with extensive colleague support helps to both reinforce knowledge and convey new information, such as device or process updates.
”
With complex robotic systems, establishing what elements to analyse can be difficult. But by utilising key performance indicators (KPIs), you can quickly and accurately track progress and identify improvement areas.
”
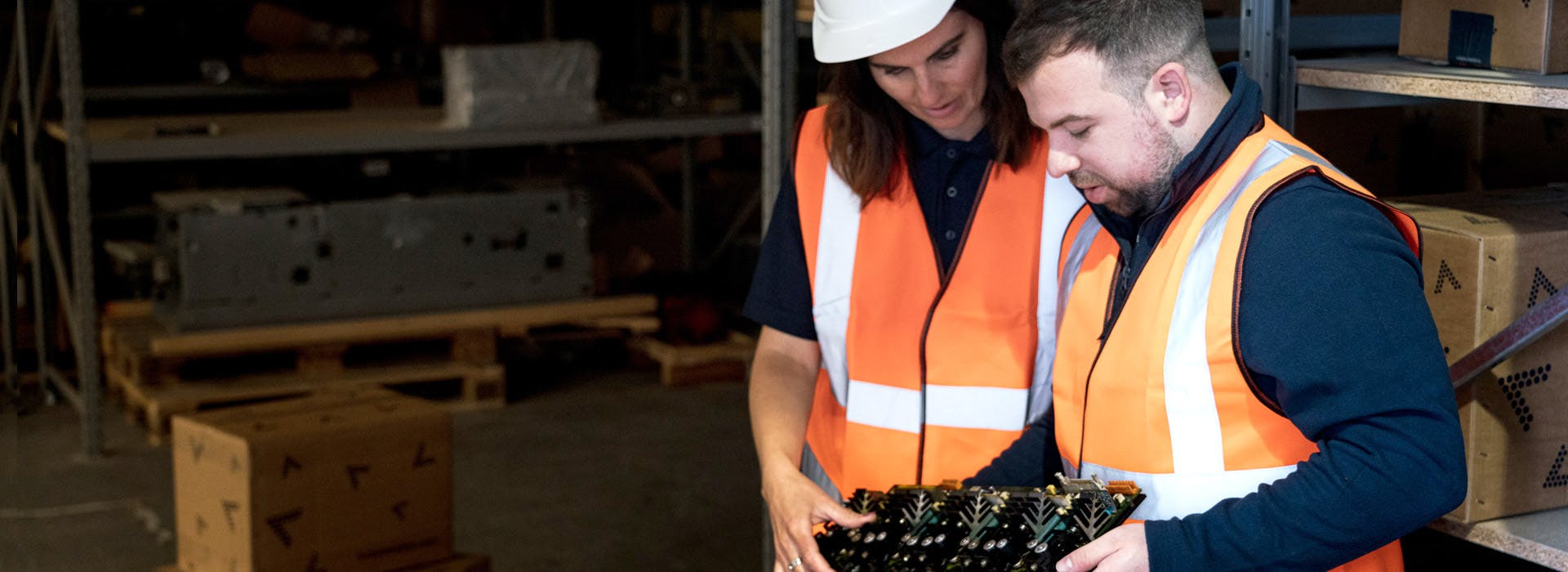
6. Project maintenance
When operating correctly, a well-designed maintenance programme should be a constant background force, working alongside production with minimal disruptions to maximise productivity. While a comprehensive plan should cover all foreseeable maintenance, unexpected breakdowns can happen. In these cases, having strong supplier backing and contingency measures can be the difference between a fast recovery or extended periods of downtime.
Develop a maintenance plan
At its core, a maintenance plan combines documentation and schedules that define the work required to keep critical equipment running. It manages all service processes, scheduling, spare parts and assets to ensure optimal performance. By providing a comprehensive framework for repairs and servicing, you can reduce significant breakdowns and combine maintenance across individual systems to lower overall downtime.
When developing your maintenance plan, there are crucial elements you should cover:
- Maintenance plan overview – The overview should describe the equipment being maintained while outlining the approximate timings. You should document all foreseeable inspection, service and calibration tasks while listing any assets (key staff, contractors, spare parts and equipment) required for the operations.
- Detailed work instructions – A vital component of the maintenance plan is documentation, including instructions, process guides and procedures. These documents may come directly from the equipment manufacturer or be produced in-house. Regardless of the source, instructions should provide competent staff members with the knowledge to conduct all operations effectively and safely. Where applicable, they must comply with relevant industry or equipment standards. This is especially true for calibration operations which require traceability.
- Comprehensive schedule – A detailed schedule is the core of any maintenance plan. It should set the exact times for all inspection, servicing and calibration tasks – while specifying how long tasks should take and the impact of the downtime on wider systems. The schedule should be regularly updated to allow for factors such as company shutdowns, public holidays and asset availability. When you create a schedule for a piece of equipment, you must consider other systems too. For example, if taking the equipment offline stops other automation, align both devices' maintenance schedules - performing the service tasks together to reduce the total downtime.
- Identify spare parts – For each automation covered by the maintenance plan, list all vital spare parts. In many cases, this information is provided by the device OEM, but additional components may need to be identified for systems with extensive integration. For regular service components, keeping suitable stock levels and replenishing them as required is essential. As part of your planning, identify a reliable automation parts supplier with a proven track record who can support your operation quickly.
- Asset management – Throughout the maintenance plan, you should list key individuals, equipment, suppliers and contractors required to carry out all inspection, service and calibration tasks. All parties should know their responsibilities and be supplied with the information needed to perform their operations effectively.
- Training – It is important to create a dedicated training programme within your maintenance plan. This should support staff in understanding the new automation, ensuring they have the relevant skills needed to undertake the service tasks. Ensure suitable time and financial resources are set aside – allowing for comprehensive training to take place with additional support to confirm the knowledge is retained. Many plans mistakenly assume that just the initial training is enough to preserve vital information. Supplying further sessions with supporting resources (such as documentation and videos) increases knowledge retention and reduces the pressure on maintenance staff.
With these elements covered, you will have a comprehensive framework to manage the assets and scheduling that facilitate service operations. But to further safeguard your automation project's maintenance, there are additional considerations beyond creating a plan – you also need a reliable spare parts supplier, suitable data monitoring and systems to ensure mistakes are learnt from.
Find a trusted parts supplier
The strength of any maintenance programme depends on having a reliable source for the critical components needed to keep robotic systems running accurately, safely and at optimal efficiency. If vital parts are unavailable, it is impossible to execute scheduled maintenance and react to emergency repairs, creating an opportunity for significant downtime, financial loss and a reduction of confidence in the automation.
When looking for a supplier, you need to find an industry-trusted vendor. Challenge potential component vendors with your specific application using strategies similar to those utilised when choosing an initial automation supplier. The first aspect to consider is the availability of spare parts – by creating a list of crucial components, you can check the current stock levels with suppliers and assess their projected stock levels. All suitable suppliers should be able to provide a background on the historical and future stock levels of your critical components.
The next important factor is the speed at which a supplier can provide components. A vendor with an extensive intercontinental distribution network has an increased ability to supply facilities across the world quickly. Suppliers with more extensive networks will also hold greater stock levels (thanks to increased storage), while a more comprehensive geographic coverage can help them source hard-to-find components. With shifting global deficiencies of fundamental materials and electronic components, spare part shortages are becoming increasingly common. Finding a supplier who will search all corners of the globe to meet your requirements is critical in preventing lengthy unexpected downtime.
Leading suppliers will also go beyond merely providing components and bring a wealth of industry knowledge that should aid your ongoing maintenance and future robotics projects. Ensure you partner with a vendor who can support all your automation requirements.
Monitor performance to predict problems
While some automation failures occur with no warning, in many cases, the issue could have been prevented through careful data and performance monitoring. By tracking critical operational parameters such as cycle time, current draw, vibration readings, communication dropouts and scrap levels, you can identify a significant failure before it occurs. What to monitor will depend on the robotic application, but the channels must be continuously measured and have appropriate alarm limits.
Well-configured alarms should alert you of unusual feedback values (or communication dropouts), increasing the chances of you catching the issues early. For example, a gradual increase in vibration levels within a CNC mill might signify mechanical play within the equipment. By implementing alarm limits, you can detect when the machine crosses a specified safe threshold and stop the process before further damage occurs. While these thresholds can be only the alarms provided by the robotics OEM, it may be beneficial to add supplementary sensors – especially in complex systems where numerous integrated devices work together.
As well as monitoring equipment operational parameters, a broader approach to metrics is also required. Using previously identified KPIs, you should actively track the overall performance of the equipment. Through continual data analysis, you can identify reoccurring patterns contributing to a loss of efficiency. For example, by evaluating the timings of unexpected shutdowns (and the cause), it is possible to detect service operations missing a critical task or if the maintenance is not occurring frequently enough to prevent failure. By analysing this data with the relevant staff, you can quickly create targeted solutions to reduce reoccurring downtime.
Audit performance and identify areas for improvement
Throughout this guide, we have stressed the importance of continually reviewing performance to identify strengths and areas for improvement. This ongoing approach helps to initialise change faster, minimise project mistakes and keep colleagues involved in your robotics operation, maintaining its success.
Regular maintenance audits with key stakeholders allow you to identify areas where measures could be deployed to improve current processes. This could include revising which spare parts are held in stock, shortening service cycles on specific devices to prevent a reoccurring issue, or providing further staff training to increase the number of individuals capable of maintaining a device.
Your project's continued analysis also helps keep colleagues involved, retaining their interest in automation. This should encourage further support for all aspects of the project going forward and improve collaboration across the business, which benefits the wider robotics effort.
Furthermore, audits create an excellent opportunity to identify the positive aspects of your maintenance operation, allowing you to turn your project into a real-world case study. Detailing how successful elements of the maintenance plan were created and deployed can help your colleagues to use similar working methods across other automation projects within the company. While the importance of analysing projects for areas of improvement is often stressed, the value of highlighting positive aspects is sometimes missed. If your maintenance plan is effective, provide others with valuable insight into how this success has been achieved and how they could apply it to their projects.
Potential maintenance errors
- Ineffective spares supplier – Nearly all modern automation systems require regular maintenance. With most service tasks requiring new components, the strength of your spares supplier will directly affect your facility's total efficiency. When selecting a component vendor, use recognised specialists with the knowledge and network to support your robotics application.
- Wasting data – Metrics captured through modern automation systems and additional sensors can be harnessed to implement alarm thresholds (used to prevent device failures) and identify improvement areas. Be sure to utilise all data available to you.
- Lack of coverage – A common mistake is for knowledge relating to critical maintenance tasks to remain with a small group of individuals – an error often fuelled by the extensive periods between some maintenance tasks. It is essential to create information deposits independent of personnel. Producing comprehensive maintenance instructions and training a larger pool of staff creates greater knowledge redundancy.
- Poor scheduling – When creating schedules, sufficiently allow for the time and costs incurred maintaining the automation. Where possible, you should always align service tasks with co-existing systems to reduce facility downtime.
- Not valuing operators – When planning and discussing automation maintenance, the staff working closest to the device can be missed too often. Be sure to consult with your operators and teams regularly working with the equipment, as they may bring valuable foresight.
”
The strength of any maintenance programme depends on having a reliable source for the critical components needed to keep robotic systems running accurately, safely and at optimal efficiency.
”
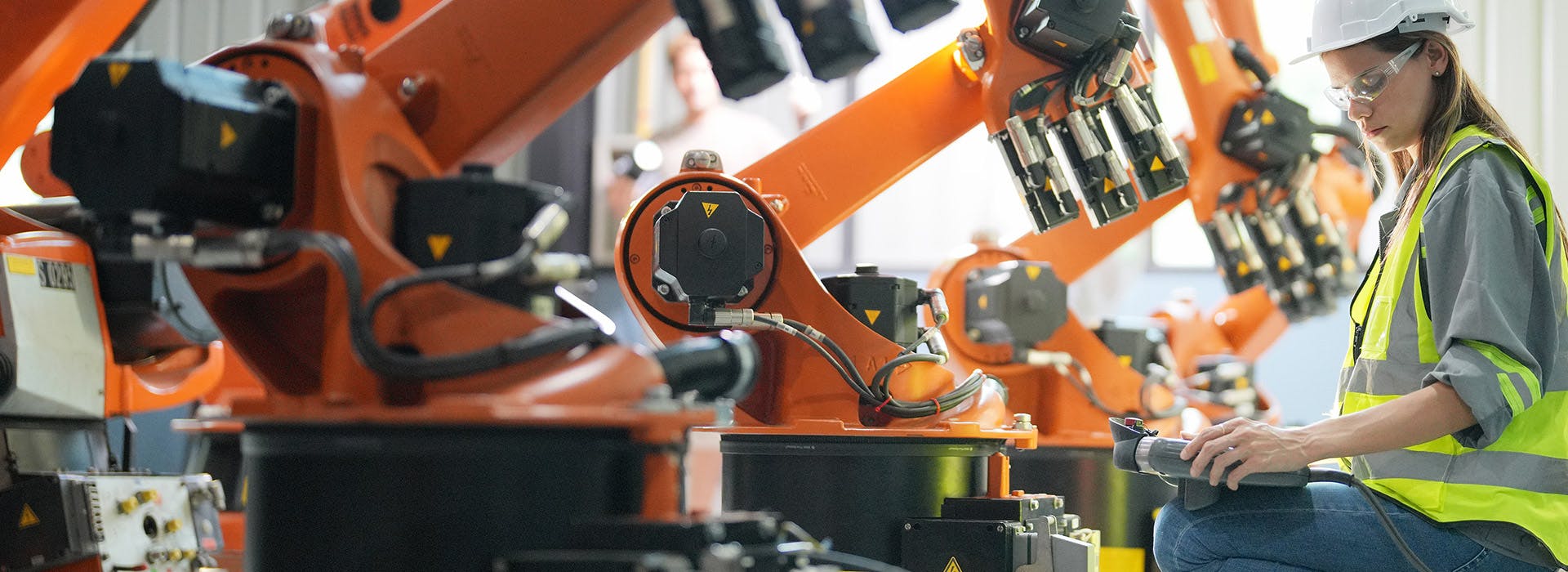
7. Conclusion: Making the most of automation adoption
The widespread adoption of robots and automation across manufacturing is a testament to the benefit it can bring. Many organisations have recognised that such equipment can provide an immense operational advantage, allowing them to work more flexibly, accurately and efficiently, and positively impact the bottom line. And as concepts such as collaborative robots, AI-based systems and machine vision continue to progress, so the uptake of robots and automation will continue to increase.
But as this guide has shown, adopting automation requires a systematic approach to preparation, implementation, operation, monitoring and maintenance to give the process the best outcomes. When managed in a methodical and structured manner, with effective communication across disciplines, automation adoption can be a harmonious and energising experience.
The power of partnership should also be deployed to maximum effect. Robotic OEMs are keen to establish collaborative relationships with end users to ensure their equipment works optimally. And global parts suppliers such as EU Automation can provide expert guidance and advice around areas such as monitoring and maintenance, helping end users alleviate any potential problems that could cause downtime before they occur. And these organisations can also help end-users identify parts requirements to keep robotic systems in perfect working order. This service extends to tracking down hard-to-find components to keep production lines running.
In short, industrial automation and robotics provides fantastic opportunities for business improvement and profitability. And by working in tandem with specialist organisations committed to the highest levels of customer service, you can ensure your company remains on the road to long-term success.
Sources:
[1] https://www.statista.com/statistics/1219772/industrial-automation-market-size-worldwide/
[2] https://www.reuters.com/article/us-boeing-777-idUSKBN1XO17C
[4] https://www.theverge.com/2018/4/13/17234296/tesla-model-3-robots-production-hell-elon-musk
[5] https://hbr.org/2012/09/ten-reasons-people-resist-chang
[6] https://www.theguardian.com/technology/2016/feb/26/mercedes-benz-robots-people-assembly-lines
Explorer d'autres secteurs
Pour vous inspirer.
inspirez
inspirez
inspirez
Recevez régulièrement des actualités et de vraies informations sur l'automatisation directement dans votre boîte de réception.